2024年問題や人手不足に対応!RGVを活用した搬送効率化のポイント | 搬送ロボットガイド
AMR
2024年問題や人手不足に対応!RGVを活用した搬送効率化のポイント
公開:2025.04.09 更新:2025.06.02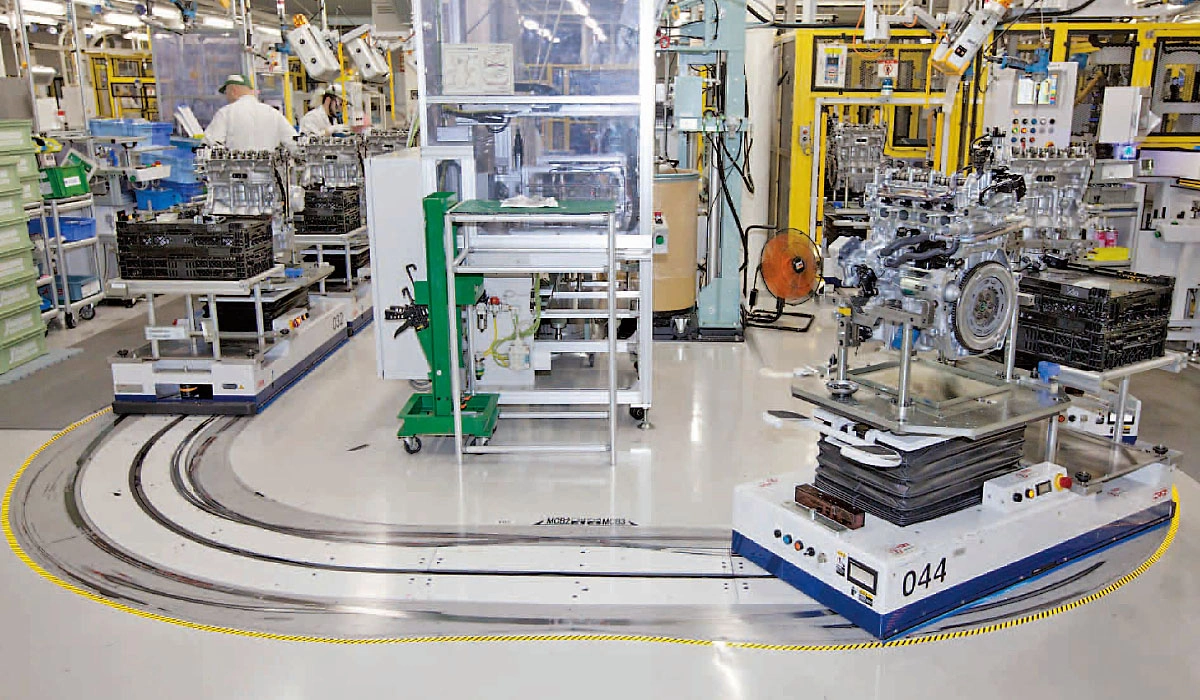
人手不足や在庫管理の複雑化、物流の2024年問題を背景に、搬送効率化が課題となっています。これに対し、レール上を走る無人搬送車RGVの導入が進み、搬送精度向上やコスト削減に成功している事例も見られます。
目次
生産や流通現場における搬送の課題とは?
生産や流通の現場では搬送の効率が求められますが、現実にはさまざまな障害が存在します。人手不足や管理の複雑化、制度の変更など、企業が解決すべき課題は非常に多岐にわたります。ここでは、それぞれの具体的な課題について解説します。
◇労働力の不足
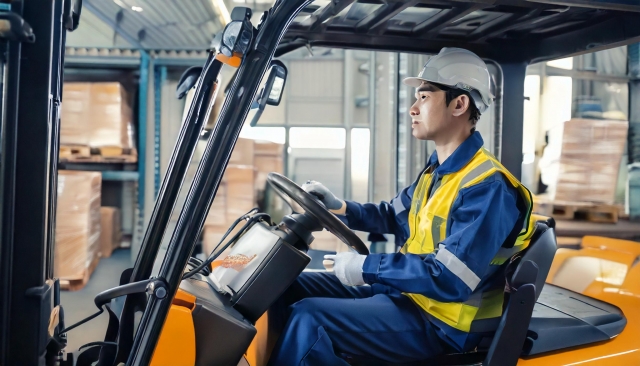
現在の日本の労働環境において、欠かせない問題が労働力と人材の不足です。少子高齢化が進むなか、生産や物流の現場では深刻な人手不足が発生しており、国内の40%以上の大企業・中小企業が経営課題として人手不足を挙げています。
流通現場では、特にフォークリフト運転手、倉庫作業員、トラックドライバーなどの人材確保が困難な状況です。労働力が不足すると搬送作業の効率が低下し、納期遅延のリスクが高まります。また、既存の従業員の負担が増え、作業ミスや事故の発生リスクも上昇します。
さらに、経験豊富なベテラン作業員が減少することで、搬送の品質や管理能力が低下するのも課題です。このような状況を改善するため、近年では自動搬送ロボット(AGV)や無人搬送システム(AMR)の導入が積極的に進められています。
◇在庫管理の課題
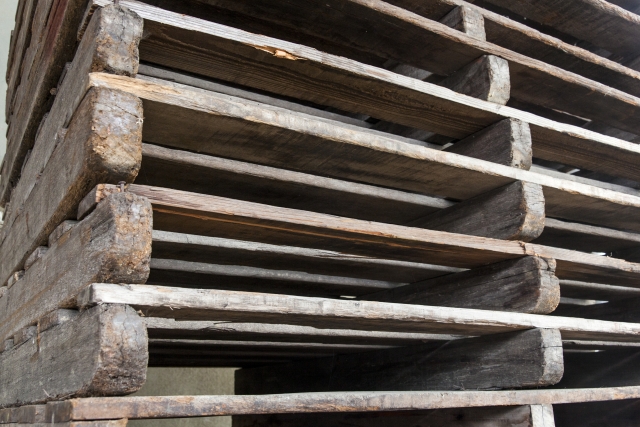
生産工場や物流センターでは、多種多様な原材料や部品、製品を適切に管理する必要があります。しかし、製品のバリエーションが増えるほど在庫の種類も増加し、管理が複雑になります。特に、部品が数万点にも及ぶ製造業では、必要な部品を迅速にピッキングできる仕組みを構築するのは容易ではありません。
在庫管理が適切に行われないと、欠品や過剰在庫が発生し、生産計画に影響を及ぼす可能性があります。また、在庫スペースの最適化も重要な課題であり、限られた倉庫スペースを効率的に活用しなければなりません。こうした背景から、近年ではIoT技術を活用したリアルタイム在庫管理システムの導入が進んでいます。
◇2024年問題
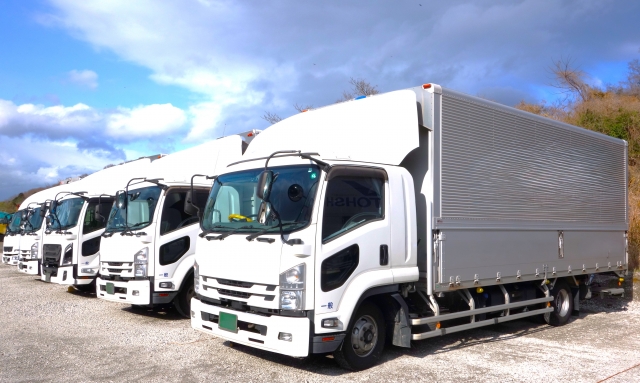
2024年問題とは、働き方改革関連法によりトラックドライバーの時間外労働が年間960時間に制限されることによって生じる物流業界の課題です。この制限により長距離輸送のリードタイムが長期化し、従来のような柔軟な配送が難しくなる可能性があります。
さらに、輸送コストの上昇も避けられません。ドライバー不足のなかで規制が強化されると、運送会社は運賃の引き上げを余儀なくされ、結果として製造業や小売業のコスト負担が増大します。また、荷主側にも影響がおよび、配送スケジュールの見直しや共同配送の活用が求められます。
特に、時間指定配送の制限や納品頻度の低下が進めば、サプライチェーン全体の見直しが必要となるでしょう。
◇煩雑な返品作業
物流の現場では返品対応も大きな課題のひとつです。小売業におけるEC市場の拡大に伴い、返品件数が急増しており、それに対応する作業負担が増えています。
返品された製品に対しては、状態の確認、再販の可否判断、再入庫、仕分け、再梱包、再出荷などのプロセスが必要です。しかし、これらの作業は煩雑であり、物流の効率を大きく低下させる可能性があります。また、返品の増加は在庫管理にも影響を及ぼし、リアルタイムで在庫データを更新する必要があります。
【あわせて読みたい】
▼人手不足解消へ!清掃業界でAMRロボット導入の効果と活用法
RGVとは?特長と活用シーンをわかりやすく
日本が抱える労働力不足や高齢化社会を踏まえると、現代の生産現場や物流センターにおいて、より効率的な搬送システムの導入が一層重要となっていることは間違いありません。特に、無人搬送車(AGV)の活用は、作業の自動化や作業員の負担軽減、安全性の向上に大きく貢献しています。
以下では、AGVの一種であるRGVについて詳しく説明します。
◇RGVとは
RGV(Rail Guided Vehicle)とは、レールに沿って移動する無人搬送車のことです。AGVとは異なり、RGVは移動経路が固定されたレールに沿って走行するのが特徴であり、この特性により安定した搬送が可能となります。特に、工場や倉庫、物流センターなどで活用され、精密なルートをたどる必要がある環境において効果を発揮します。
RGVは通常、リニアモーターや車輪を使って、レールに沿った正確な移動を行います。これにより、荷物や部品を効率的に搬送でき、従来の手作業や自動搬送システムと比べて作業効率が大幅に向上します。
◇バッテリーが不要
RGVの大きな特徴のひとつは、バッテリーが不要であることです。一般的なAGVはバッテリーで動作するため、定期的な充電が必要ですが、RGVはレールに設置された電力供給システムを利用します。これにより、バッテリーの残量を気にすることなく、24時間連続して稼働することが可能です。
バッテリーの交換や充電設備の整備といった手間が省けるため、運用コストが大幅に削減されるだけでなく、常に安定した稼働が求められる生産現場や物流センターにおいて大きなメリットとなります。さらに、充電インフラの設置を必要としないため、場所に制約されず、規模の大きな施設でも柔軟に導入できます。
◇レールの設置が必要
RGVはレールに沿って移動するため、事前にレールの設置が不可欠です。この点が、バッテリーを使用しないAGVとの大きな違いです。
レールは施設内の決められた経路に設置され、これにより車両の走行ルートが固定されます。レールを配置する際には、設置場所の計画が重要であり、後からレールの変更や追加を行うことは難しく、また導入コストも高くなりがちです。
しかし、特定のルートで高精度な搬送を行う必要がある場面では、安定した動作を確保できます。また、レールに沿った走行が確立されているため、障害物を避けるためのセンサーや回避システムを簡略化でき、システムの安定性が高まるのもメリットです。
◇重量物の搬送に向いている
RGVは、特に重量物や大型部品を搬送するのに適しています。強力なモーターと耐荷重設計により、非常に重い荷物を効率的に運搬することが可能です。これにより、フォークリフトやクレーンといった他の搬送手段と同様の役割を果たしながら、無人で運用できる点が大きな利点です。
特に、自動車産業や重機、電子機器製造業などで重い部品や完成品を扱う場面では、RGVはその優れた性能を発揮します。また、重量物を運ぶ場合、搬送中に荷物が動いてしまうリスクもありますが、RGVは横ブレのない安定した走行が可能であり、人手による搬送に比べて作業の効率が格段に向上し、安全性も高まります。
【あわせて読みたい】
RGVの導入で20%のコスト削減に成功
製造業において、効率的な生産ラインの構築は企業の競争力を左右する重要な要素です。特に、近年では環境負荷の低減や作業者の安全性向上が求められており、従来のコンベア方式に代わる新たな搬送システムの導入が進んでいます。
ここでは、小型自動車用エンジンの生産ラインにRGVを導入し、大幅なコスト削減を実現した成功事例をご紹介します。
◇エンジンの生産ラインにRGVを導入
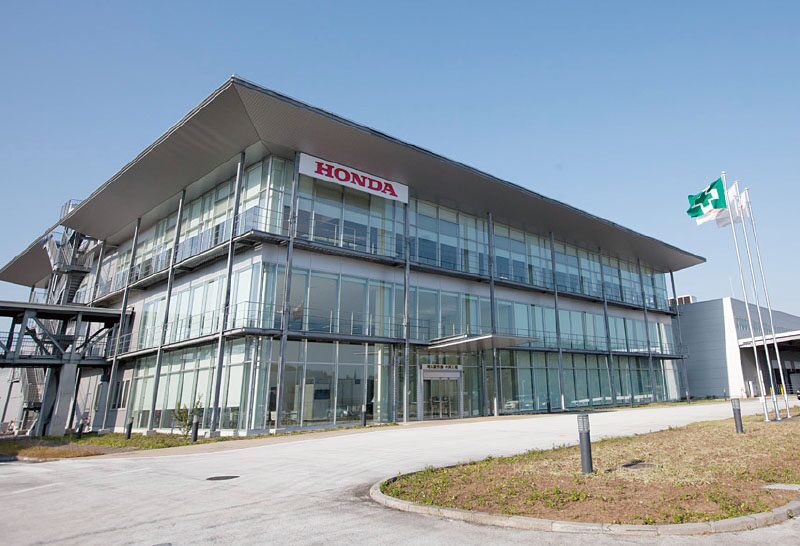
今回ご紹介するのは、小型自動車用エンジンの鋳造・加工・組み立てを一貫して行う混合生産工場において、RGVを導入して成功を収めた事例です。
この工場はもともと1日あたり約1,000基のエンジンを生産できる能力を持っていましたが、従来のコンベア方式からRGVを活用した搬送システムへと移行しました。その結果、無駄な動線の削減と柔軟な搬送が可能となり、大幅なコストダウンを実現しました。
さらに、低騒音設計や空調・採光の工夫により、作業者にとって快適な職場環境も実現されました。この取り組みは国内外から注目を集め、同工場への工場見学が相次いでいます。
◇蛇行工程で組み立てる
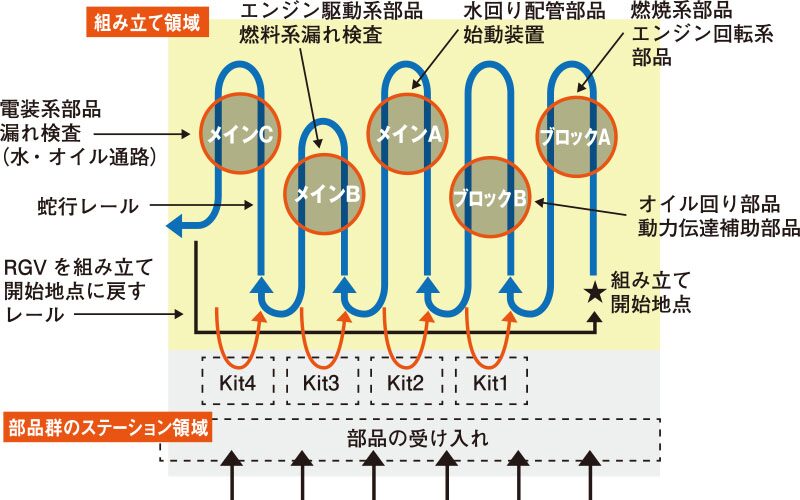
この工場における生産ラインの特徴のひとつが、RGVによる蛇行工程です。搬送ルートは「ブロックA → ブロックB → メインA → メインB → メインC」という順番で組み立て工程を進めており、RGVはこのルートに沿って正確に移動します。
従来の直線的なラインでは、工程ごとの配置を最適化することが難しく、スペースの有効活用が課題でした。しかし、蛇行工程を採用することで、作業エリアを効率的に分割し、無駄なスペースを減らすことに成功しました。
この工場では、同型のRGVが100台以上導入され、全体の搬送を効率的に管理しています。
◇静かで安全な環境を実現
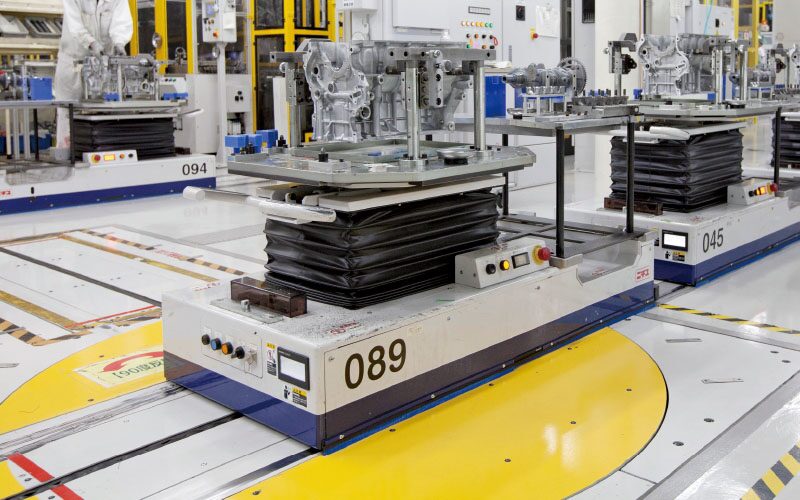
RGVを導入したことで、工場内の騒音レベルは約70dBと低く抑えられました。これは、一般的な生産ライン(80~85dB)と比べて明らかに静かであり、作業者の負担軽減にも貢献しています。騒音の低減により、作業員同士のコミュニケーションが取りやすくなり、集中力を維持しやすい環境が整いました。
また、安全性の向上も大きなポイントです。従来のコンベアはパレットが常に動き続けるため、不意に手を挟まれるリスクがありました。しかし、RGVは前方に安全センサーを備えており、障害物を検知すると自動で減速・停止する仕組みになっているため、事故の危険性も非常に少ないです。
◇20%のコスト削減
RGVの導入により、この工場では2年間で全体の生産コストを約20%削減することに成功しています。従来のコンベア方式では、チェーンの伸びや摩耗によるメンテナンス費用がかかっていましたが、RGVではその負担が大幅に軽減されました。
さらに、一般的なAGVと比較すると、RGVはバッテリー交換が不要であり、運用コストを抑えることができます。AGVは約1年半ごとにバッテリー交換が必要となり、その費用や交換作業の負担が生じますが、RGVはその必要がないため、長期的なコストパフォーマンスが非常に高いことが評価されています。
【あわせて読みたい】
安全性向上と労働環境の改善!AMR導入事例
近年、製造業や物流業界では自動化が急速に進んでおり、その中でもAMR(自律移動ロボット)の導入が注目されています。以下では、AMRの基本的な特徴や、AGV・RGVとの違い、労働環境や生産フローの改善に与える影響について、具体的な事例を交えながら解説します。
◇AMRとは
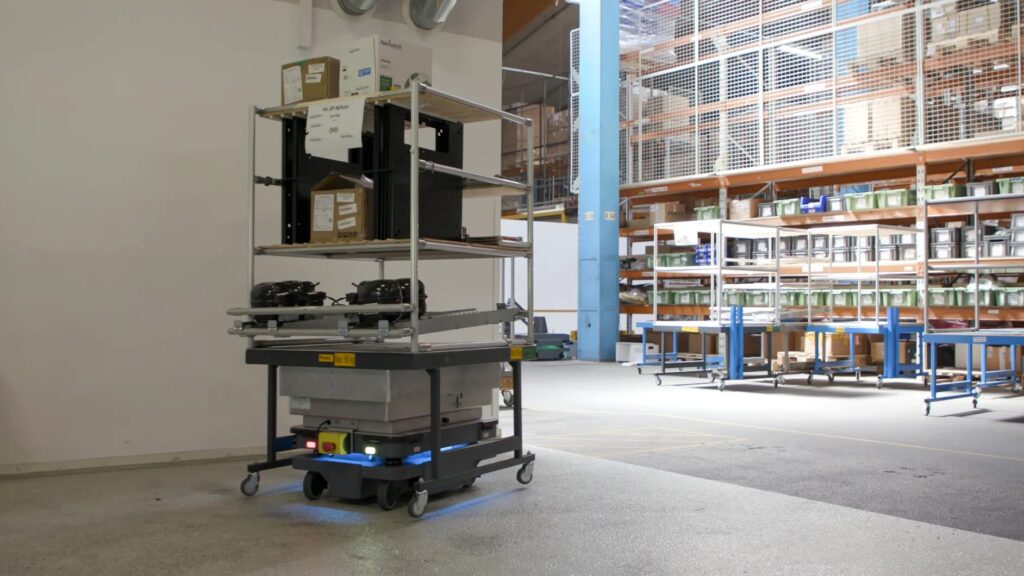
AMR(Autonomous Mobile Robot、自律移動ロボット)とは、センサーやAIを活用して自ら最適なルートを判断しながら移動する搬送ロボットです。AMRは周囲の状況をリアルタイムで認識し、障害物を回避しながら目的地へ移動します。そのため、環境の変化に強く、柔軟な運用が可能です。
また、AMRは導入時のインフラ整備が最小限で済む点も大きなメリットです。これらの特性から、AMRは製造業だけでなく、物流倉庫や医療機関など、さまざまな分野で導入が進んでいます。
◇AGVやRGVとの違い
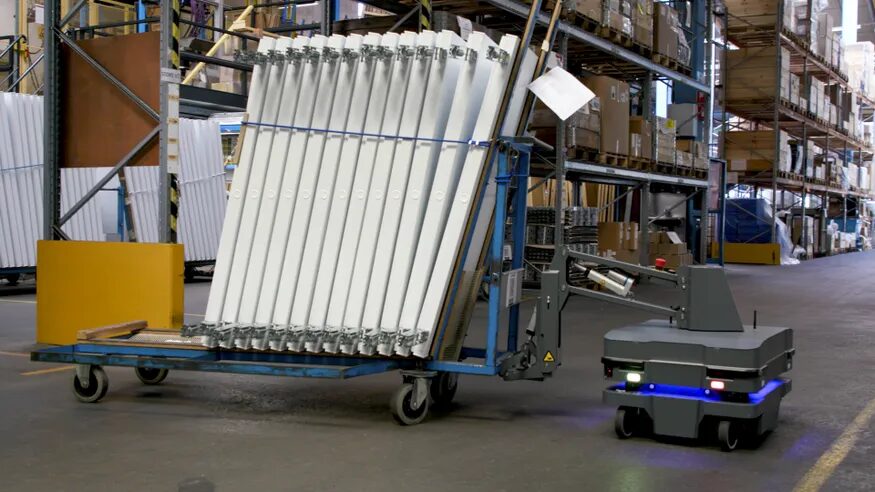
AMRとAGV・RGVの最大の違いは、その移動方式と柔軟性にあります。AGVは、磁気テープや床面のマーカーを頼りに決められたルートを走行します。そのため、障害物があると停車するしかなく、新しいルートを設定するにはシステムの改修が必要です。
一方、RGVはレール上を走行する搬送車で、高速かつ大量の搬送が可能ですが、設置コストが高く、レイアウト変更が困難というデメリットがあります。
これに対してAMRは、センサーやカメラ、AIで周囲を認識し、最適なルートを判断しながら障害物を回避して目的地へ到達できます。この適応能力により、変化の多い生産現場や物流倉庫でもスムーズな搬送が可能です。
◇安全性と労働環境の改善
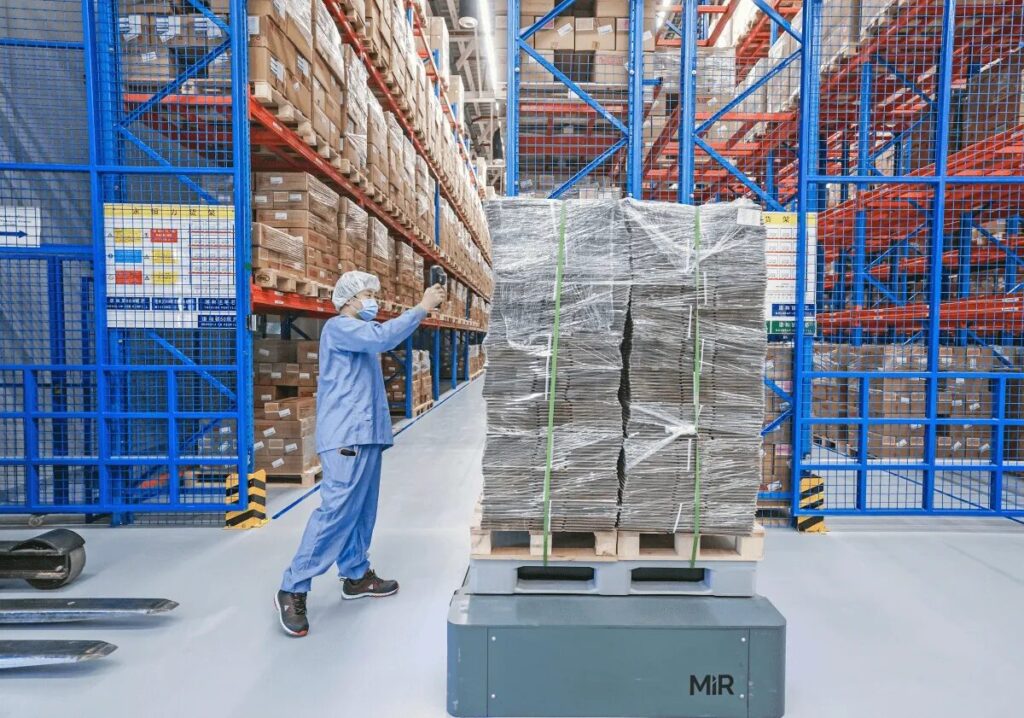
デンマークにあるVestfrost Solutions A/S社は、AMRの導入により成果を上げた企業のひとつです。同社は製薬・食品業界向けに冷蔵・冷凍製品を製造しており、約200名の従業員が日々200ユニットを生産しています。
同社が直面していた課題は、資材や製品の運搬作業が従業員にとって大きな負担となっていたことです。特に注目すべき点は、1人あたりの移動距離が1日で50kmに達していたことでした。
この問題を解決するため、同社はAMR(自律移動ロボット)「MiR」を導入。現在では5台のMiRが工場内の資材搬送をすべて担い、従業員の負担は大幅に軽減され、事故リスクも低減しました。
◇生産フローの改善
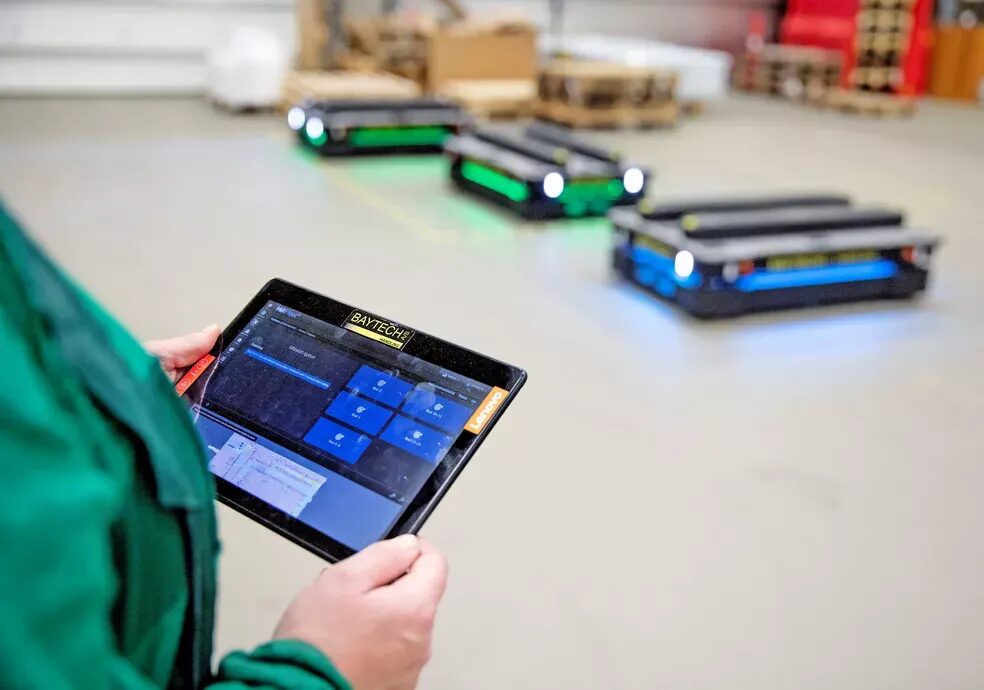
同社のAMR導入によるもうひとつの大きな成果は、生産フローの最適化です。従来は3台のトラックで行っていた搬送業務がMiRロボットに置き換えられたことで、人と車両の動線が整理され、作業の効率が向上しました。
現在では、工場内搬送の約80%をAMRが担っており、従業員は移動に費やしていた時間を本来の作業に充てられるようになりました。ロボットによる自動搬送が、生産現場の合理化と省人化を後押ししています。
【あわせて読みたい】
▼FOOD展でロボットの製造体験!驚きの結果とロボット技術の可能性
搬送作業を自動化するメリットとは?
近年、製造業や物流業界における競争が激化するなか、効率化やコスト削減が企業の重要な課題となっています。特に、搬送作業は多くの産業で重要な役割を担っており、従来の手作業による搬送方法から自動化へのシフトが進んでいます。
以下では、搬送作業の自動化がもたらす主なメリットについて詳しく説明します。
◇付加価値の高い業務へのシフト
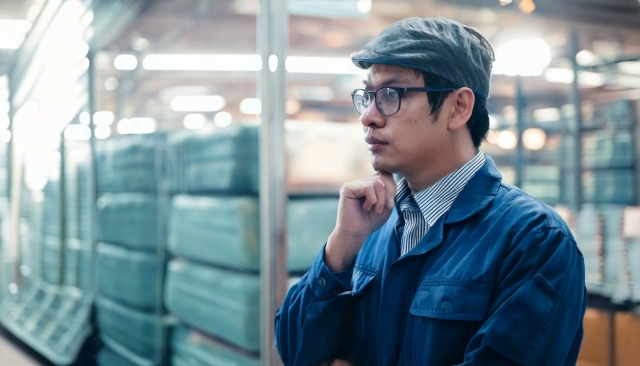
搬送作業を自動化する大きなメリットのひとつは、作業員が単純で反復的な作業から解放され、より高度な業務や付加価値の高い仕事に時間を割けることです。
例えば、品質管理やプロセス改善、設備のメンテナンス、工程の最適化といった業務に集中できるようになり、企業全体の競争力が向上します。また、自動化により、作業員の役割が単調な業務から戦略的な業務へとシフトすることで、モチベーションが高まり、企業全体の生産性向上にも寄与します。
作業員が専門的な知識やスキルを活かせる環境が整うことで、企業の成長にもつながるでしょう。
◇作業スピードの安定
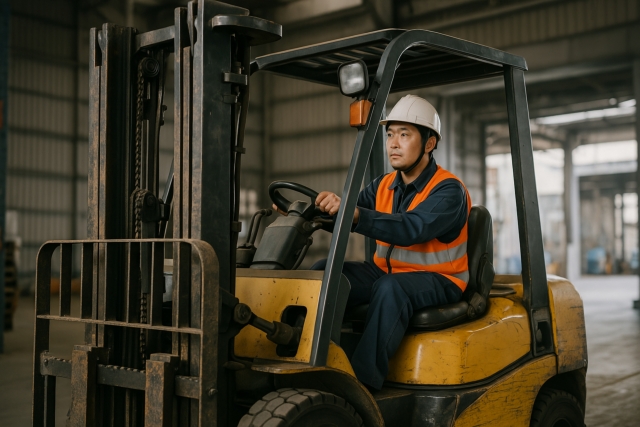
常に一定のスピードで効率的な動作が実現することも、自動搬送システムの重要なメリットです。人力による搬送作業では、作業員の体調や気分、疲労度によって作業スピードが変動することがありますが、自動化によりそのような変動を排除できます。
さらに、搬送作業の時間が安定することで、納期や生産計画の予測精度が向上し、業務の進捗状況を常に把握できるようになります。また、無駄な待機時間や遅延を減らすことで、全体的なコスト削減にも貢献します。
◇作業ミスの減少
搬送作業において最も重要な課題のひとつが「人為的ミス」です。例えば、荷物の積み間違いや誤配送は、生産ラインの遅延や品質の低下を引き起こし、最終的には顧客満足度にも影響を及ぼす可能性があります。
しかし、搬送作業を自動化することで、事前に設定されたルートや動作パターンに従って正確に荷物を搬送できるため、ヒューマンエラーによる誤配送や積み間違いが起こりにくくなります。また、システム内で動作を監視するセンサーやカメラ、AIを活用することで、万が一のトラブルにも迅速に対応でき、問題を未然に防ぐことが可能です。
作業ミスの削減により、製品やサービスの品質が安定し、企業の信頼性向上にもつながります。
◇作業員の負担軽減
搬送作業の自動化により、作業員の負担が大きく軽減されることも重要なポイントです。特に、重い物を運んだり、長時間同じ作業を繰り返したりすることは、作業員にとって身体的・精神的な負担となります。
しかし、自動化された搬送システムでは、こうした肉体的な負担を機械が肩代わりするため、作業員はより快適で安全な環境で働けます。さらに、単調な作業の繰り返しによる疲労感や体力的なストレスも軽減されるため、作業員の健康が守られ、ケガのリスクも減少します。
厳しい労働環境の改善は、単に身体的・精神的な負担を軽減するだけでなく、作業員が安心して働ける職場づくりにもつながる重要な要素です。快適で安全な環境は、作業効率の向上を促すだけでなく、従業員のモチベーションやエンゲージメントを高め、長期的な人材の定着や生産性向上にも大きく寄与します。
【あわせて読みたい】
AMRの導入を考えるなら検討したいおすすめメーカー3選
AMR(自律移動ロボット)の導入を検討する際には、信頼性と実績を兼ね備えたメーカーの選定が非常に重要です。ここでは、AMR分野で特に注目を集めている3つの企業を取り上げ、それぞれが持つ強みや優位性を解説します。
◇大喜産業株式会社
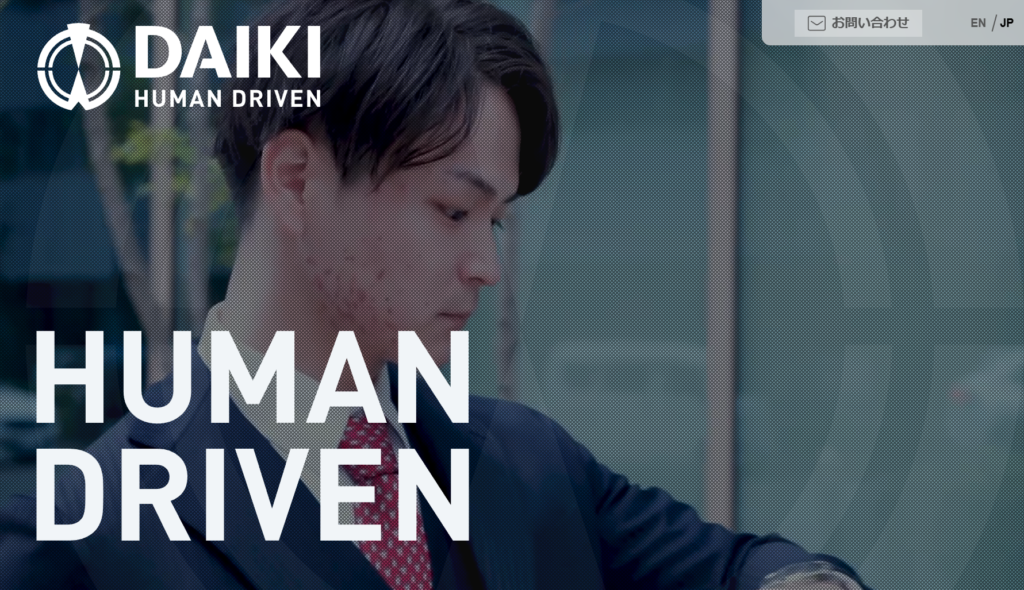
大喜産業株式会社は、ロボティクス事業、伝動機器事業、産業機器事業、設備機器事業の4分野を中心に事業を展開している企業です。近年は特に、自律搬送ロボットや協働ロボットなどを扱うロボティクス事業に注力しています。
同社の強みは、さまざまなメーカーのロボットを取り扱い、顧客のニーズに最適な自動化ソリューションを多数提案できる点にあります。AMRにおいても、OnRobotの自動化プラットフォームを搭載した「PallBot」や、デンマーク企業の自律移動型ロボット「MiR」など、先進技術を取り入れた製品を提供しています。
会社名 | 大喜産業株式会社 |
営業本部 | <住所> 〒550-0012 大阪府大阪市西区立売堀1-5-9 <電話番号> 06-6541-1987 |
営業本部東京オフィス | <住所> 〒100-0004 東京都千代田区大手町1-5-1 大手町ファーストスクエア4F <電話番号> 03-5219-1463 |
大阪支店 | <住所> 〒550-0012 大阪府大阪市西区立売堀1-5-9 <電話番号> 06-6532-0751 |
東京支店 | <住所> 〒333-0815 埼玉県川口市北原台3-2-21 <電話番号> 048-297-1388 |
東京支店つくばオフィス | <住所> 〒305-0031 茨城県つくば市吾妻1-5-7 ダイワロイネットホテルつくば2F <電話番号> 029-817-4844 |
名古屋支店 | <住所> 〒452-0805 愛知県名古屋市西区市場木町416 <電話番号> 052-505-8201 |
東大阪支店 | <住所> 〒581-0861 大阪府八尾市東町4-1 <電話番号> 072-997-0123 |
京滋支店 | <住所> 〒520-3047 滋賀県栗東市手原3-2-3 <電話番号> 077-553-6155 |
四国支店 | <住所> 〒761-0301 香川県高松市林町2554-1 <電話番号> 087-868-4511 |
九州支店 | <住所> 〒812-0895 福岡県福岡市博多区竹下2-4-7 <電話番号> 092-441-0198 |
営業時間 | 公式サイトに記載なし |
公式ホームページ | https://www.daiki-sangyo.co.jp/ |
なかでも「MiR」は、標準的なカートやコンテナの搬送から、特殊なサイズや形状の物品に対応可能なオプションまで備えており、国内外の多くの企業に採用されているAMRとして注目を集めています。
大喜産業株式会社について詳しく知りたい方はこちらも併せてご覧ください。
▼MiR社の魅力的なMiR製品とその販売代理店・大喜産業とは
さらに詳しい情報は公式ホームページでも確認できます。ぜひチェックしてみてください。
◇オムロン株式会社
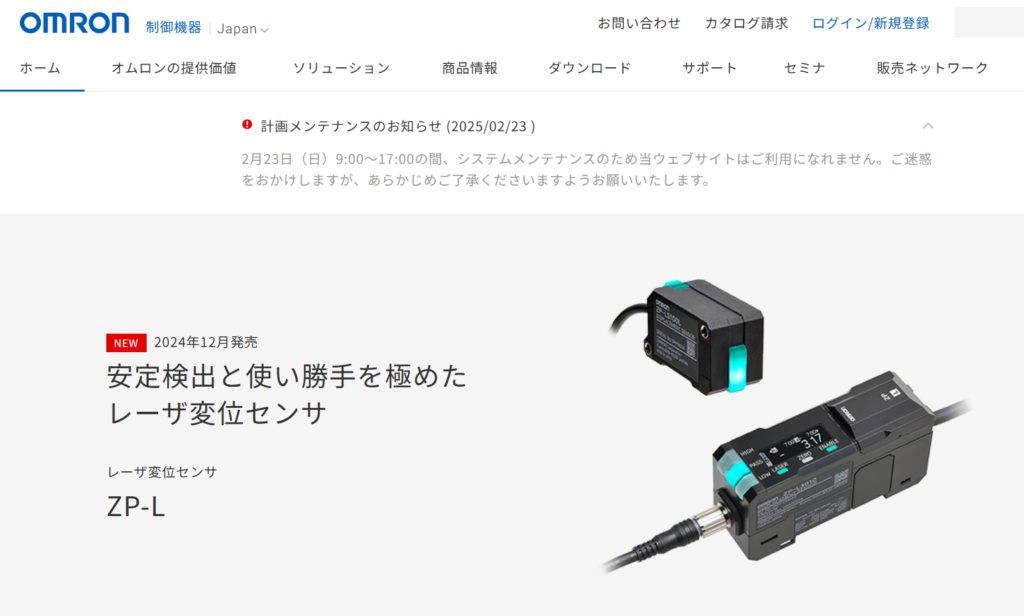
オムロン株式会社は、制御機器や電子部品、社会システムなど、幅広い分野で事業を展開している企業です。特に、工場の自動化(FA)や医療分野における高い技術力と豊富なサービスを持っています。
オムロンのロボティクス事業では、モバイルロボット、協調ロボット、産業用ロボットなどを提供しており、特にモバイルロボットにおいては、大規模な一括管理システムを提供している点が特徴です。
会社名 | オムロン株式会社 |
所在地 | 〒600-8530 京都市下京区塩小路通堀川東入 オムロン京都センタービル |
電話番号 | 075-344-7000 |
営業時間 | 公式サイトに記載なし |
公式ホームページ | https://www.fa.omron.co.jp/ |
同社のAMRはラインアップも豊富で、可搬重量は150kgから1.5トンまで対応しており、非常に柔軟な用途に対応できます。また、同社はAMRを初めて導入する事業者向けに、「モバイルロボット オンライン・オプションセミナ」も提供しています。
オムロン株式会社について詳しく知りたい方はこちらも併せてご覧ください。
▼オムロン「LD-250」の特徴とは?製造業の課題に技術で立ち向かう
◇アルテック株式会社
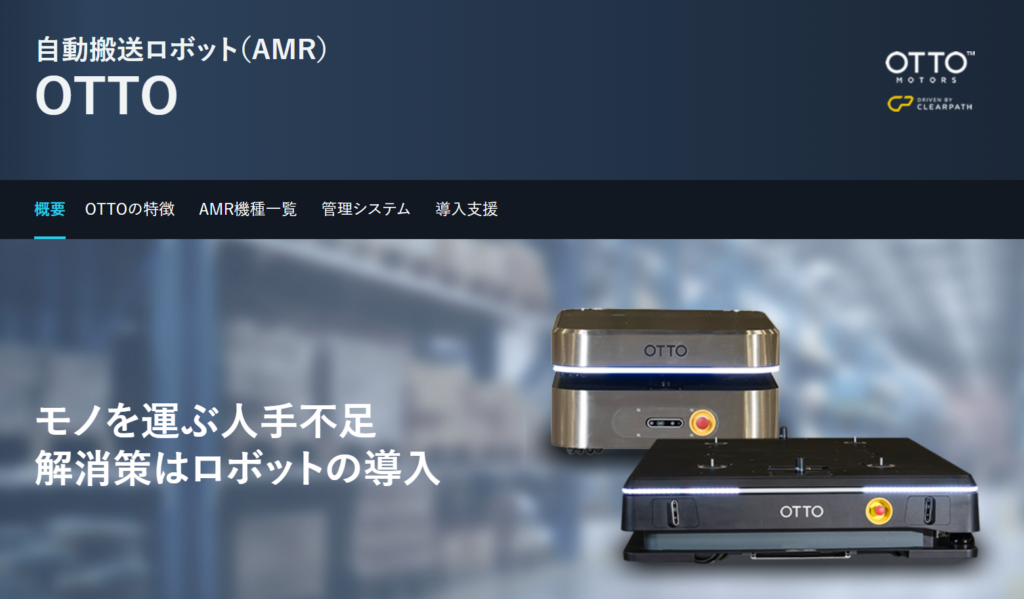
アルテック株式会社は、主に産業機械の輸入販売を専門とする商社です。同社の大きな特徴は、グローバルネットワークを活かし、国内外の選りすぐりのロボット機器を提供していることです。
AMRにおいては、カナダのClearpath Robotics社が提供する「OTTO」シリーズを日本に導入しており、日本市場での先駆けとして注目されています。「OTTO」シリーズは、可搬重量が異なる4つのモデルをラインアップしており、最大1.9トンまでの荷物運搬が可能です。
会社名 | アルテック株式会社 |
所在地 | 〒104-0042 東京都中央区入船2-1-1 住友入船ビル2F |
電話番号 | 03-5542-6760 |
営業時間 | 公式サイトに記載なし |
公式ホームページ | https://smart-logistics.altech.jp/amr/otto/ |
さらに、「OTTO」シリーズはカスタマイズアタッチメントの開発が可能であり、現場ごとのニーズに応じた専用アタッチメントを自由に設計・連携させることができます。
アルテック株式会社について詳しく知りたい方はこちらも併せてご覧ください。
▼OTTO MotorsのAMRの特徴と可能性!日本での普及が期待される理由
生産や流通現場では搬送の効率化が求められますが、実際にはさまざまな課題があります。まず、少子高齢化により人手不足が深刻化し、特にフォークリフト運転手やトラックドライバーの確保が困難になっています。これにより作業効率が低下し、ミスや事故のリスクも増加しています。この問題を受け、自動搬送ロボット(AGV)や無人搬送システム(AMR)の導入が進められています。
次に、在庫管理の複雑化も課題です。製品の多様化により管理が難しくなり、欠品や過剰在庫のリスクが高まっています。これに対応するため、IoTを活用したリアルタイム在庫管理が普及しつつあります。
さらに、2024年問題によりトラックドライバーの時間外労働が制限され、輸送コストの上昇や配送の柔軟性低下が懸念されています。物流現場では返品対応も煩雑化しており、作業負担の増大と在庫管理への影響が課題となっています。
こうした背景を踏まえ、無人搬送車であるRGV(Rail Guided Vehicle)の導入が注目されています。RGVはレール上を移動するため高精度な搬送が可能で、バッテリー不要、長時間稼働が特徴です。特に重量物搬送に適しており、自動車産業などで活躍しています。ある工場では、RGV導入により搬送の無駄を削減し、コストを20%削減する成功例も報告されています。
この記事を読んでいる人におすすめ
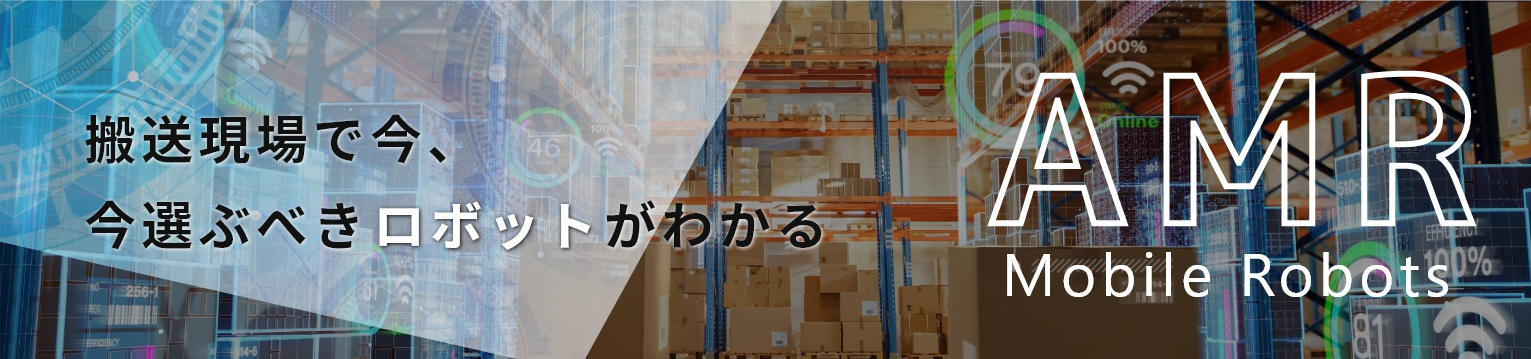