GTPとAMRロボットの違いは?規模やニーズによって最適な選択をしよう | 搬送ロボットガイド
AMR
GTPとAMRロボットの違いは?規模やニーズによって最適な選択をしよう
公開:2024.05.27 更新:2024.10.07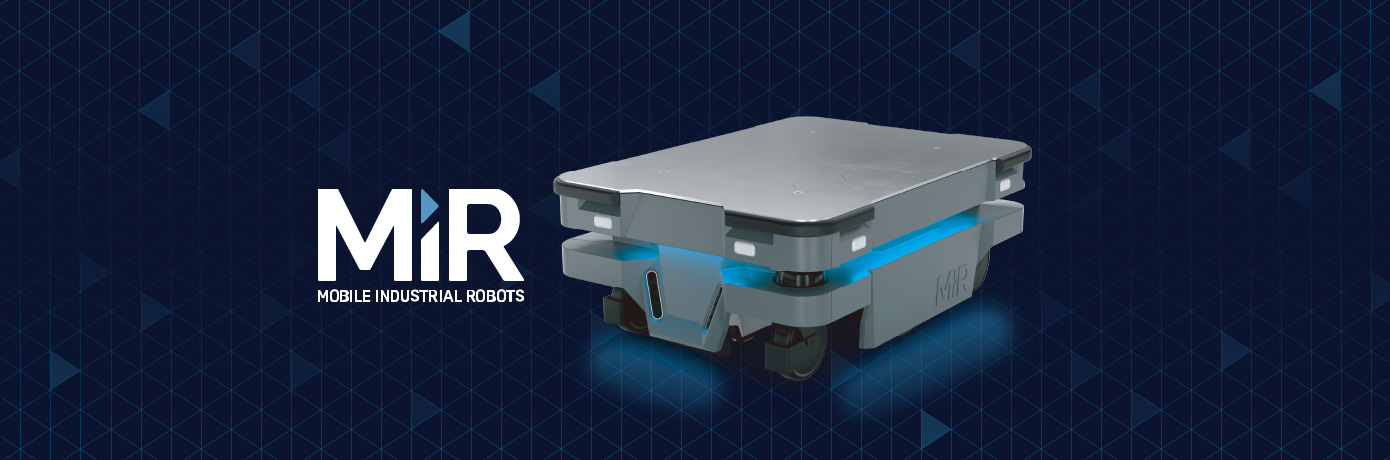
物流業界で注目されているロボットとしてAMRとGTPがあります。導入する際には、それぞれの特徴を知っておくことでより適したロボットを採用できるでしょう。
GTPは、ロボットや自動運搬車を使って商品を作業員のもとに運ぶシステムで、大規模な倉庫や流通センターで効果を発揮します。一方、AMRは倉庫内の移動経路を自律的に計画するため、狭いスペースや複雑なレイアウトにも柔軟に対応できるのです。
導入コストや運用方法に違いがあるため、企業の規模やニーズに応じた最適な選択が求められます。
目次
GTPとは?棚搬送型ロボットの利点
物流業界で注目されるGTPシステムは、従来のピッキング方法とは異なる自動化技術です。こちらでは、GTPシステムの特徴とその利点について詳しく解説します。
◇GTPの特徴
GTP(Goods to Person)システムは、物流や倉庫管理の自動化技術の1つであり、ロボットや自動運搬車(AGV)を活用して、商品を保管場所からピッキング作業を行う作業員のもとに直接運ぶ仕組みです。従来のPerson to Goodsシステムでは、作業員が倉庫内を歩き回って商品を取りに行く必要がありましたが、GTPシステムでは商品が自動で作業員の元に運ばれるため、作業員は移動する必要がありません。
GTPシステムは異なるサイズや形状の商品の取り扱いにも柔軟に対応でき、リアルタイムで在庫情報や作業進捗を把握できるため、効率的な在庫管理が実現します。
◇GTPの利点
GTPシステムの最大の利点は作業効率の向上です。商品が直接作業員の元に運ばれるため、倉庫内を移動する時間が削減され、ピッキング作業のスピードが大幅に向上します。自動化されたシステムによりピッキングミスや在庫の取り扱いミスが減少し、作業の正確性が向上するのも利点です。これにより、作業員の肉体的な負担が軽減し、安全性も向上します。
さらに、GTPシステムは需要に応じて柔軟に対応できるため、業務量や季節変動に対するスケーラビリティが高いです。結果として、作業効率の向上と人為的ミスの削減により運営コストが低減し、スペースの効率的な利用によって倉庫の運営費用も削減されます。
物流現場で求められる「歩かない」ピッキングとGTPの課題
物流現場において、作業者の歩行を削減することは生産性向上の鍵です。こちらでは、歩かないピッキングシステムの重要性とGTPの導入に関する課題について見ていきます。
◇物流現場で「歩かない」が求められる理由
物流現場において多くの時間を占めているのは、作業者が倉庫内を歩き回ることです。広大な倉庫内で1日に何キロも歩くことも多く、その間に作業者は必要な商品を探し出してピッキングします。これには多くの時間と労力がかかるため、作業効率と生産性が低下してしまうのが課題です。
そのため、歩行距離や時間を短縮することは、物流現場における生産性向上の点で非常に重要となります。そのため、歩かないピッキングシステムであれば、作業効率の向上だけでなく、歩行の負担が減ることで作業者の疲労も軽減できるのです。
◇GTPの課題
GTPの導入に際しては、高い導入コストが課題の1つとして挙げられます。新しいシステムの導入には、設備や機器の購入、システムの構築など、多額の費用が必要です。また、従来のピッキング方法と異なるシステムの導入の際には、倉庫の設計や配置の変更も必要になります。
さらに、作業者のトレーニングや新しいシステムへの適応に時間がかかる可能性があることも懸念点です。GTPの導入でこれらの課題を克服するためには、慎重な計画とリソースの適切な割り当てが求められます。
GTPとAMRどちらが適している?それぞれに適したケースについて
GTPとAMRは、物流業界において生産性と作業効率の向上に貢献する重要な技術です。どちらも異なる利点と制限を持っているため、規模や状況に応じた適切な選択が必要となります。
◇GTPが適している場合
GTPは、大量の商品を保管している倉庫内でのピッキング作業を効率化するシステムです。そのため、特に大規模な倉庫や流通センターにおいて効果を発揮します。例えば、オートストアは数万から数十万の商品を保管できる大規模な倉庫に適したGTPシステムです。
GTPはAmazonをはじめとする大手企業でも採用されており、作業の効率化、スケーラビリティ、作業の正確性といった面で高い効果を発揮しています。
◇AMRが適している場合
AMRは、GTPと比較して倉庫内の移動経路を自律的に計画し、商品を運搬できるのが特徴です。自己学習および環境への適応性が高く、狭いスペースにも順応し、必要な場所に素早く移動できます。そのため、倉庫内でのピッキング作業や搬送経路がより複雑で多様なレイアウトを必要とする場合には、GTPよりもAMRが適しているといえるでしょう。
また、導入コストが高いGTPに比べ、AMRは比較的導入しやすいという利点もあります。倉庫の規模や作業の特性に応じて、導入コストを抑えつつ自動化を実現したい場合には、AMRがより適しているかもしれません。
GTP導入で作業者の負担軽減と倉庫の容積効率向上
同じGTPの導入でも、企業ごとにその目的や意図は異なります。こちらでは、GTP導入の事例を紹介します。
◇労働環境改善を目指した事例
寝具メーカーの西川ロジスティクス株式会社は、GTPを21台導入しています。これまで西川ロジスティクス株式会社では、広い倉庫内を従業員が歩き回りながらピッキング作業を行っていましたが、重い寝具や寝装品を扱うため、重労働となってしまうことが課題でした。
この労働環境を改善すべく導入したのが、自動棚搬送ロボット「Ranger GTP」です。Ranger GTPは、ロボットが物流施設の床を走行し、専用の棚を移動させて商品を担当者の元まで運ぶシステムです。これにより、ピッキングや棚入れの際に従業員が倉庫内を歩き回る必要がなくなり、労働負荷が軽減されました。
◇物流ロボットの連携で更なる自動化を目指す
テキスタイル物流株式会社は、繊維製品や生地の保管・出荷・加工・企画・OEMなどを手がけており、現在は物流ロボット「EVE」を88台導入しています。物流ロボットとチルトトレイ式仕分け装置を連携させており、さらなる効率化を実現している点が特徴です。
この連携により、従業員は倉庫内を歩き回ることなく効率的なピッキングが行え、仕分けも自動で可能となります。この新しい物流システムの導入により、従来は100人で行っていた出荷業務を20人体制に軽減できているのです。
GTP(Goods to Person)システムは、物流や倉庫管理の自動化技術であり、ロボットや自動運搬車(AGV)を利用して商品を作業員の元に運ぶ仕組みです。従来のPerson to Goodsシステムと異なり、作業員が倉庫内を歩き回る必要がなくなります。これにより、ピッキング作業のスピードが向上し、在庫管理の効率も高まるのです。
GTPの導入には高い初期コストがかかりますが、作業効率の向上と人為的ミスの削減により運営コストが低減されます。また、GTPシステムは柔軟性が高いため、大規模な倉庫や流通センターに適しているといえるでしょう。
一方で、AMR(Autonomous Mobile Robots)は、倉庫内の複雑なレイアウトにも適応できるため、より多様な環境に対応できます。GTPとAMRは、物流業務の特性に応じて選択することが重要です。
導入事例として、西川ロジスティクス株式会社はGTPを導入した結果、労働負荷を軽減し、効率的なピッキングを実現しています。
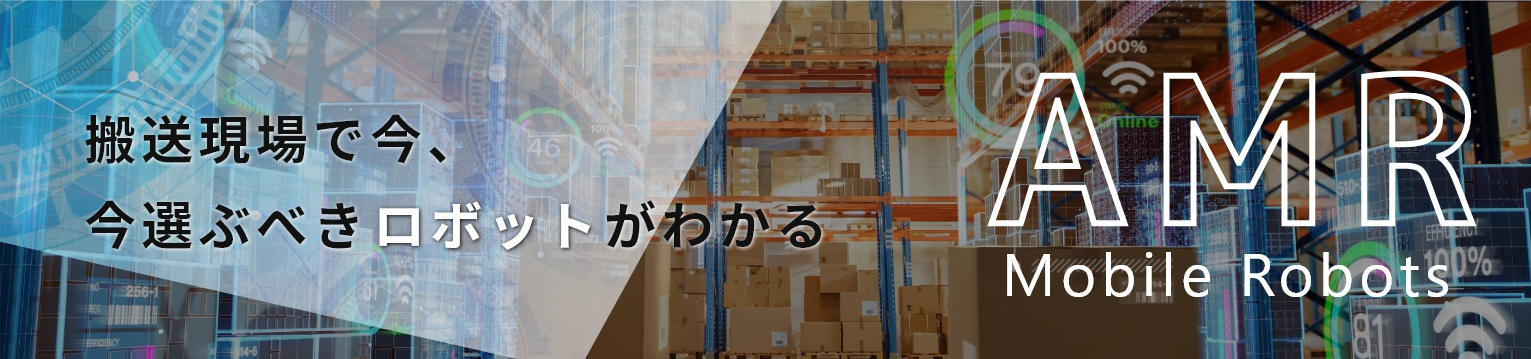