構内物流の課題とは?エレベーターも使用できるAMRロボットの開発で作業時間大幅削減 | 搬送ロボットガイド
AMR
構内物流の課題とは?エレベーターも使用できるAMRロボットの開発で作業時間大幅削減
公開:2024.04.25 更新:2024.10.07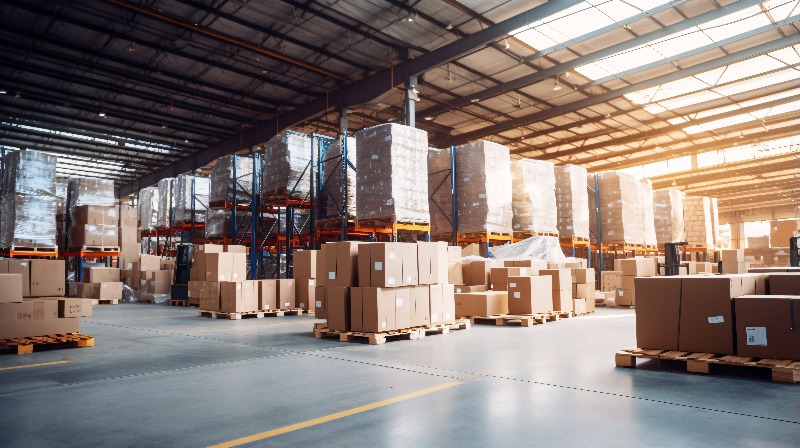
構内物流は製造業における重要な業務であり、工場内での物流活動を指します。生産性向上が肝要な中、構内物流は直接生産性に貢献しないとみなされる傾向がありました。しかし、エレベーターを使用可能なAMRロボットの開発により、環境の変化に柔軟に対応し、レイアウト変更や新しいルートの追加にも即座に対応できるようになりました。
目次
見直され始めている工場内の搬送作業
物流について一般的に考えると、多くの人は企業同士や企業と顧客の間の流れを思い浮かべるでしょう。しかし、物流は企業内や工場内でも重要です。これを構内物流と呼び、その見直しが進んでいます。では、構内物流について説明しましょう。
◇後回しにされがちだった搬送作業の見直し
製造業では、生産性が最も重要であり、製品に付加価値を与えることが肝要です。そのため、構内物流などのモノの移動に対しては、直接生産性に貢献しないと見なす企業が少なくありませんでした。
例えば、工場内で必要なアイテムがどこにあるかが不明確であったり、必要以上にアイテムが生産ラインに供給されていたりすると、作業過多や生産過剰が発生し、生産性が低下します。これらの問題は多くの工場で発生しており、その結果として生産性が低下することに繋がります。
こうした、直接生産性に結びつかない課題は、多くの企業で先送りされる傾向があります。
◇構内物流について
構内物流とは、製造業における重要な業務のひとつであり、工場の敷地内で行われる物流活動を指します。時には生産物流とも呼ばれるこのプロセスは、製品の生産に不可欠です。
製造業の工場では、さまざまな部品や材料が倉庫から製造現場へと移動します。これらの移動は、製品の組み立てや加工を行うための必要な段階です。構内物流を効率的に行うことは、工場全体の生産性や効率を向上させる上で極めて重要です。
例えば、正確な部品や材料の供給が行われず、作業現場での待ち時間や生産ラインの停止が発生すると、生産性が低下します。また、効率的な在庫管理や作業フローの最適化を通じて、構内物流を改善することで、生産プロセス全体の効率化が図られます。その結果、生産性向上やコスト削減などの利点がもたらされることが期待されます。
構内物流の課題とは?AGVによる搬送作業の課題
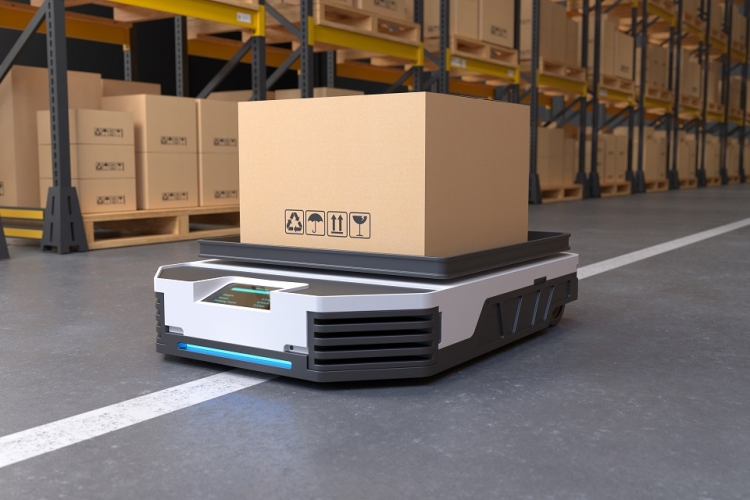
引用元:株式会社トヨコン
製造業の工場では、構内物流が非常に重要であることを既に紹介しました。そんな重要な構内物流における課題は、どのようなものがあるでしょうか。構内物流において特に重要な役割を果たすのが、無人搬送ロボットであるAGVです。そして、このAGVが直面する課題こそが、構内物流全体の課題と言えるでしょう。
◇構内物流の課題
構内物流には、仕入先からの材料や部品の受け入れや保管、在庫管理、生産指示に基づくピッキングなど、さまざまな作業が含まれます。これらの作業は、物を移動させる搬送作業が必要なため、工場内での生産活動にとって欠かせないものです。
構内物流にはいくつかの課題があり、具体的には以下のようなものが挙げられます。
受け入れ・入庫
構内物流では、フォークリフトや台車を使ってパレットを運搬することが一般的です。この運搬作業は時間と労力を要し、作業員の負担が大きくなります。また、目視による検品が必要なため、ミスの可能性も高まります。
保管
資材の保管状態を正確に管理する必要があります。手作業で管理する場合、正確性やリアルタイム性が課題となることがあります。
ピッキング・配膳
ピッキング作業が手作業で行われる場合、ミスが発生するリスクがあります。また、配膳のタイミングを調整しないと、後続の工程に遅れが生じる可能性があります。そのため、作業効率の向上が求められます。
◇AGVによる搬送作業の課題
AGVは、あらかじめ始点と終点を設定し、磁気テープなどのガイドラインに沿って走行するシステムです。工場の搬送作業に使用される事も多く、作業の手助けとなることもありますが、ニーズに合わせてフレキシブルに製品の製造を進める上で、課題もあります。
この方法ではガイドラインの設置されていない場所にはアクセスできないため、これまで到達が難しかった箇所には到達できません。そのため、新たな経路への変更を行うには、ガイドラインの再設置や施設の変更が必要です。
製造ラインが多品種少量生産を行う工場では、製品の種類が頻繁に変わります。製品の変更に伴い、各工程で使用する資材や部品、工具を入れ替える必要があります。しかし、AGVはこのような柔軟性の高い自動搬送を実現するのが難しいのです。
AMRによる搬送で自動搬送を可能に
構内物流において、AMRを用いた自動搬送は有効な手段といえます。特に多品種少量生産を行う工場の構内物流においては、自律移動ができるAMRは大変有効といえるでしょう。
◇構内物流にAMRがおすすめの理由
AMR(自律走行型ロボット)は、固定的なルート制約なしに動作し、基点さえ設定すれば自由に駆け回り、ジョブを自動でこなします。この柔軟性は、構内物流において特に有用です。
なぜなら、AMRは環境の変化に適応し、レイアウトの変更や新しいルートの追加に対応できるからです。従来のAGVと比較すると、ガイドレールやマーカーなどの設置が不要であり、変更したレイアウトを自動で認識し、最適な経路を計算します。
このような特性により、AMRは人の代替が難しい作業においても活躍します。例えば、繊細な品物の運搬や、複数の作業ステーション間の素早い移動など、高度な物流作業に適しています。
さらに、AMRは人手不足の解消にも役立ちます。人手が不足している状況下では、効率的で柔軟な自動化が求められます。AMRはその要求に応えるだけでなく、作業環境の変化にも柔軟に対応するため、構内物流において重要な役割を果たします。
◇AMRの工場内での活用例
AMR(自律走行型ロボット)は、様々な物流業務において活躍する可能性があります。例えば、製造中の搬送では、作業者が半製品をAMRに乗せ、目的地に運ばせることで、作業者は組み立てに集中できます。また、ワークセル生産方式では、作業者が必要な材料をAMRに指示し、自動で運搬させることで、作業者のパフォーマンスを維持できます。
組み立てラインへの配送では、AMRが大型のコンポーネントを運び、ライン作業者に供給します。ピッキング作業では、作業者がピッキングした商品をAMRに載せ、荷揃え場まで運ばせることで、作業者の負担を軽減できます。完成品の搬送では、AMRがパレットを移動させることで、生産ラインの最終地点から目的地までの搬送を効率的に行えます。
これらの活用事例を通じて、AMRが物流業務において人手不足の解消や作業効率の向上に貢献できることが分かります。 AMRは単純作業から人を解放し、作業者がより高度な業務に集中できるよう支援します。
エレベーターも使用出来るAMRの開発で課題を解決
AMRは構内物流において優れた活躍が期待出来ますが、ある工場では製造現場の移動する際に上下階を行き来する必要がありました。この課題を解決するため、AMRが自らエレベーターに乗って移動を可能にする開発が進められました。
◇工場に合った自動搬送システムの必要性
ある工場では、工程間の搬送に台車を使っていました。製品を積んで後工程へ運び、空になった台車を持ち帰るという手順でした。ただし、次の工程までの距離がかなり長く、この往復は作業者にとって大きな負担でした。
初めはAGVによる搬送を検討しましたが、通路幅の制限があり実現できませんでした。そのため、狭い通路でも走行できるAMRが最適と判断され、そのシステムの構築が進められました。
◇エレベーターを使用出来るAMRの開発
AMR(自律走行型ロボット)を工場内でエレベーターを利用できるようにするためには、エレベーターとの連携が必要です。一般的に、最新のエレベーターは外部連携機能を備えていますが、この工場のエレベーターはそのような機能を持っていませんでした。
そこで、AMRの制御PCとエレベーターの制御盤を接続し、相互に通信する仕組みを構築が必要となりました。具体的には、AMRの制御PCがエレベーターの制御盤に指示を送信し、エレベーターの操作を行うことで、AMRがエレベーターを利用してフロア間を移動することが可能になります。
ただし、エレベーターの内部には可動部分があり、LANケーブルなどの通信ケーブルを敷設することが困難でした。そのため、可動部分を通過できる同軸ケーブルを使用し、信号変換を行って通信を行いました。
◇47kmの搬送作業を削減
AMRの導入により、工場内のエレベーター利用に関する運用面での工夫が行われました。具体的には、エレベーターの利用を「人優先」と「AMR優先」の2つに分け、それぞれの利用ターンを完全に分離して運用されています。AMRが利用中は人の操作や途中での降りることができないようにし、混乱を避けるためにシンプルな形で運用されています。
さらに、AMRがエレベーターを待つ際には積層信号灯を点灯させ、周囲の人にもAMRの利用状況を周知するようにしています。AMRはフロアを移動する際に、各階層におけるマップの切り替えを行いながら位置認識を行いますが、エレベーターとの連携を優先するため、その到着をトリガーとしてマップの切り替えが行われます。
これらの取り組みにより、試運転を経て本格運用が開始され、効果も確認されています。AMRの導入により、1日当たりの搬送距離が47km、作業時間の削減効果として1日当たり11.75時間が見込まれています。また、現場からは好評であり、定期便の追加などの要望も出ており、今後はさらなるルートの検討やAMRの追加導入などが検討されています。
製造業における構内物流の見直しは重要性を増しており、特に搬送作業の効率化が焦点とされています。従来は生産性に直接貢献しないと見なされがちでしたが、構内物流の最適化が製品の付加価値にも直結することが認識されつつあります。
構内物流の課題としては、受け入れ・入庫、保管、ピッキング・配膳などが挙げられ、これらを解決する手段としてAGVが活用されてきましたが、AGVにも課題があります。そのため、AMRが注目されており、その柔軟性や自律移動能力によって構内物流の効率化が期待されています。
特にAMRの活用例として、製造中の搬送や組み立てラインへの配送、ピッキング作業などが挙げられます。さらに、AMRのエレベーター利用が開発され、搬送作業の効率化が図られるなど、構内物流の見直しは多岐にわたる効果をもたらす可能性があります。
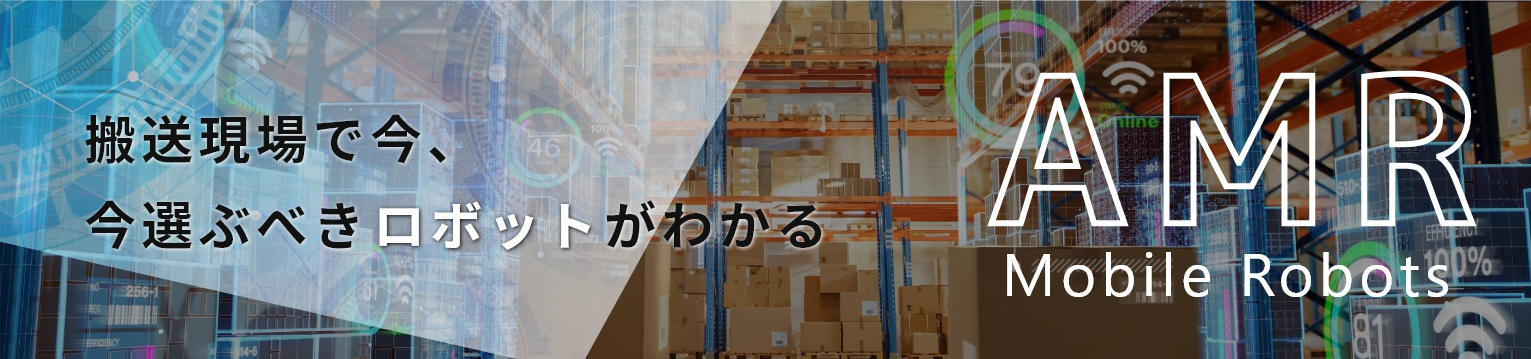