AGVの自由度が上がっている?AGVロボットの走行方式による違い | 搬送ロボットガイド
AMR
AGVの自由度が上がっている?AGVロボットの走行方式による違い
公開:2024.05.27 更新:2024.05.29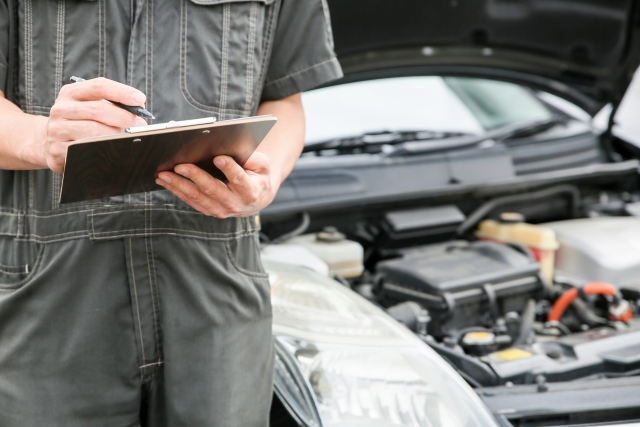
移動式ロボットの1種であるAGV(Automated Guided Vehicle)にはいくつかの課題が存在します。しかし、走行方式によって、運用する上での課題を解決できるかもしれません。
AGVは、工場や倉庫での物品搬送を自動化するための無人搬送車です。従来は磁気テープを用いた固定ルート方式が主流でしたが、これにはルート変更やメンテナンスの負担が大きいという課題がありました。
しかし、近年では新しい走行方式が登場し、AGVの自由度が大幅に向上しています。これにより、より柔軟で効率的な物品搬送が可能となり、多様な運用ニーズに応えられるようになっているのです。
目次
AGVについて解説
AGVは無人搬送車のことで、工場や倉庫などで物品の搬送を自動化するために使われる移動式ロボットの1種です。ここでは、AGVの特徴と従来のAGVとの違いについて解説します。
◇AGVとは?
AGVは、人の手を借りずに自動で指定されたルートを走行できることが大きな特徴です。これには磁気テープや光学ライン、レーザー誘導、GPSなどの技術が利用され、これらを通じて走行経路を認識し移動します。AGVは安全性も重視しており、障害物や人を感知するセンサーを備えて、安全に動作するように設計されているのです。
AGVを導入することで、人手による作業を減らし、効率的に物品を移動させられるため、労働コストや事故による損失を減少できる点が大きな強みといえます。
◇従来のAGVとは?
従来のAGVでは、磁気テープなどを使用した線路誘導式が一般的でした。これらの方式は、固定された経路を走行するためのものです。磁気テープや反射テープを床に敷設し、AGVはその上を走行します。この方式はシンプルで安価ですが、場所やルートが決まった状態で運用するため、自由度はあまり高くありませんでした。
磁気テープによる走行方式の課題
磁気テープを用いたAGVの走行方式は、固定されたルートに従って物品を自動的に搬送するために広く用いられてきました。しかし、この方式にはいくつかの課題が伴います。
◇ルート変更の際負担が大きい
磁気テープ方式のAGVは、床に敷設された磁気テープを追従して移動します。そのため、ルートを変更させる場合は既存の磁気テープを剥がし、変更するルートに沿って新しいテープを敷かなければなりません。これには大規模な作業が伴い、特に経路が複雑な場合には多くの時間と労力が必要です。
また、AGVの制御システムも新しいルートに対応するように再設定しなければならず、これも追加の時間とコストを要します。
◇メンテナンスが必要
磁気テープは、長期間使用すると汚れや剥がれが発生するため、定期的なメンテナンス(張替え)が不可欠です。床に敷かれた磁気テープが汚れで劣化すると、AGVのセンサーがテープを正確に読み取れなくなり、走行に支障をきたす場合もあります。
さらに、頻繁なAGVの走行や床の劣化によって、磁気テープそのものが剥がれやすくなる点も課題です。剥がれた部分を修復しないと、AGVが正しく走行できなくなり、誤作動の原因となります。特に高頻度で使用される経路では、テープの張替えが頻繁に必要となるため、メンテナンスコストを大幅に増加させる要因となるでしょう。
進化したAGVは走行方式も様々
従来の磁気テープによるAGV走行方式は、多くの工場や倉庫で広く採用されてきましたが、その限界が顕著になるにつれて、新しい走行方式が開発されました。こちらでは、磁気テープ走行方式に代わる進化した走行方式について説明します。
◇2次元コード方式
床や壁に設置されたQRコードやバーコードをAGVがカメラで読み取り、位置情報や経路情報を得る方式です。この方式は、2次元コードを床や壁に簡単に貼付けるだけで、新しいルートの設定ができます。また経路変更が必要な場合も、コードの位置を変更するだけで済むため、迅速な対応が可能です。
◇光学誘導方式
AGVが床に設置された反射テープやラインをカメラや光センサーで検出し、その経路に従って移動する方式です。この方式は比較的簡単に経路設定ができるため、柔軟性があります。また、カメラやセンサーを利用することで高精度な経路追従が可能です。ただし、テープの汚れや損傷による誤作動のリスクがあるため、定期的なメンテナンスが必要となります。
◇レーザー誘導方式
この方式では、AGVがレーザーセンサーを使用して周囲の環境をスキャンし、自律的に最適なルートを設定します。高い柔軟性による走行が特徴で、固定されたルートに依存せず、リアルタイムで最適なルートの選択が可能です。レーザーセンサーは周囲の障害物を正確に検知し、衝突を回避する機能を持っています。
従来のAGVの課題を解決した事例を紹介
自動車工場におけるAGVの運用は、効率性や生産性の向上に大きく貢献しますが、いくつかの課題もあります。こちらで紹介するのは、自動車工場のAGV運用の主な課題と、それを解決した事例です。
◇自動車工場のAGV運用の課題
自動車工場では、複数のAGVが同時に運行し、物品や部品の搬送を行っています。しかし、多数のAGVが同時に同一経路を走行する場合、衝突や待ち時間の発生などが避けられません。さらに、工場内でのAGVのリアルタイムな遠隔監視が困難であり、衝突や渋滞などのトラブル発生時の早期対応が難しくなります。
大規模な工場や複数の生産ラインを持つ工場では、無線LANシステムの構築には高額なコストがかかる点も課題です。
◇SmartHopの活用により課題を解決
AGV運用における課題を克服した事例として、新型AGVであるSmartHopを導入した日産自動車株式会社の栃木工場が挙げられます。日産自動車株式会社の栃木工場では、以前までAGVの導入台数が多いことで走行面での問題が頻繁に発生していました。この課題を解決するために新たに導入したのがSmartHopです。
SmartHopは、従来の無線LANシステムよりも設置コストを大幅に削減できる画期的な無線システムとなります。この無線システムの導入によって、遠隔でAGVを管理できるようになり、AGVの現在位置や渋滞・衝突の有無、バッテリー残量、センサーの異常などをリアルタイムでチェックできるようになりました。
さらに、以前は緊急停止したAGVに対処するためにスタッフを1名配置していましたが、SmartHopの導入によって人による対処も不要になりました。
AGV(Automated Guided Vehicle)は、工場や倉庫で物品の自動搬送を行う無人搬送車です。指定ルートを磁気テープや光学ライン、レーザー誘導、GPSなどの技術を利用して走行します。
従来のAGVは磁気テープを使用した固定ルート方式が一般的で、ルート変更やメンテナンスに大きな負担がありました。しかし、進化したAGVでは、2次元コードや光学誘導、レーザー誘導など柔軟な走行方式が採用されています。
日産自動車株式会社の栃木工場では、SmartHopという無線システムを導入したことによって、リアルタイムでのAGV管理が可能となり、衝突回避や緊急対応が改善されました。SmartHopは設置コストを削減し、人手を減らす効果もあります。
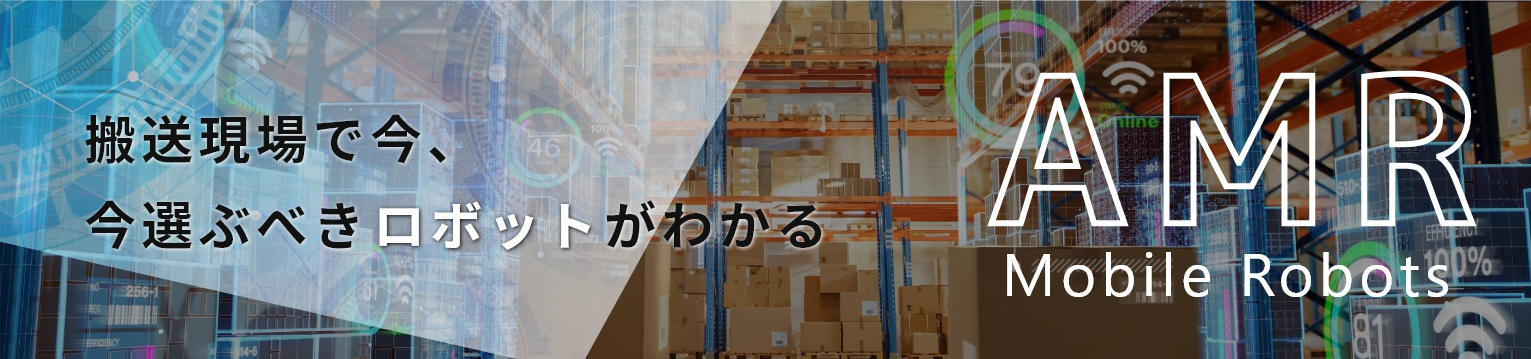