AMRでピッキング作業の時間短縮を実現するソリューション | 搬送ロボットガイド
AMR
AMRでピッキング作業の時間短縮を実現するソリューション
公開:2024.12.16 更新:2024.12.09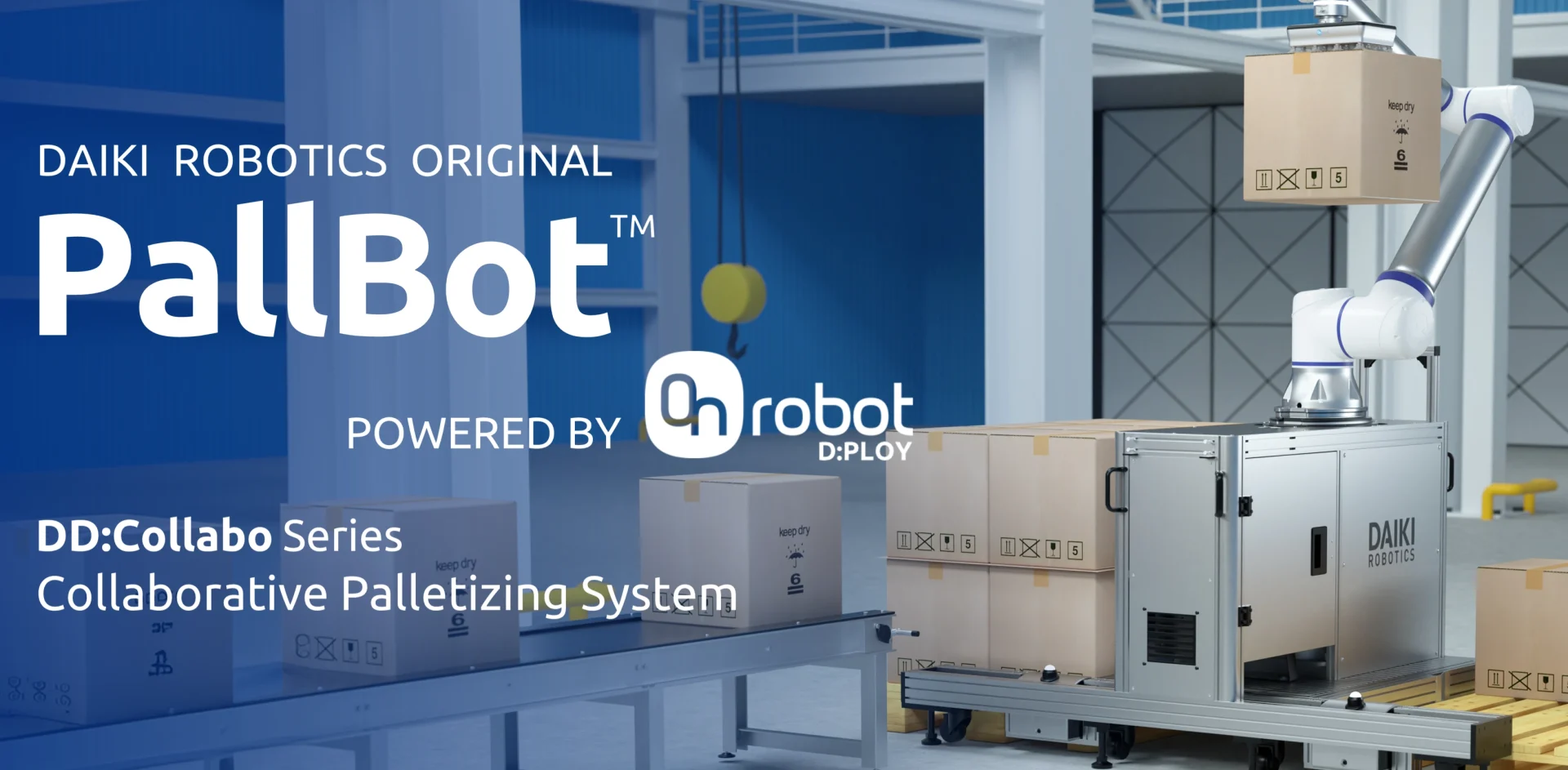
AMR(自律走行搬送ロボット)は、カートピッキングの作業効率を大幅に向上させ、作業者の負担やヒューマンエラーを減少させます。導入により、作業時間が短縮され、生産性向上やコスト削減が実現可能です。また、PallBotは導入時間を90%削減し、柔軟な運用が可能です。
目次
AMRでピッキング作業の時間短縮と課題解決
AMR(自律走行搬送ロボット)は、人や障害物を回避しながら目的地まで自動で移動できるロボットで、特に物流や製造業において注目されています。従来の作業方法と比べて、AMRは作業効率を大幅に向上させると期待されています。
◇従来のピッキングの問題
カートピッキングは、物流倉庫や倉庫業務で広く用いられている従来のピッキング方法です。この方式では、作業者がカートを押しながら、必要な商品を一つ一つ選び、指定された場所まで運びます。カートを押しながら商品をピックアップしていくという単純な作業のように思えるかもしれませんが、実際には作業者にとってかなりの負担がかかる作業です。
特に、長時間にわたる移動や、重い商品を取り扱うことが頻繁に求められるため、作業者は肉体的に非常に疲れることになります。このような負担が積み重なることで、作業の効率も低下し、最終的に物流センター全体の作業スピードに影響を及ぼすことになります。
さらに、作業者が疲れてくることでミスが発生しやすくなり、作業の品質が不安定になる原因にもなります。
また、カートピッキングには他にも多くの課題が存在します。まず、作業にかかる時間が非常に長く、効率的に商品を選び出して運ぶことが難しい点です。作業者は何度も倉庫内を移動する必要があり、移動だけで多くの時間が消費されます。商品をピックアップして運んだ後には、確認作業も必要です。
商品の数や種類を間違えないように確認を重ねるため、どうしても無駄な時間が増えてしまいます。加えて、作業者の歩行距離が長くなることで、商品の取り間違いや場所を間違えるなどのヒューマンエラーが発生する確率も高くなります。このようなミスが起きると、再確認や修正のために余分な時間がかかり、作業全体のスピードがさらに落ちてしまいます。
また、カートピッキングにかかる時間と手間が多くなることで、人件費も高くなりがちです。作業者が多くの時間をかけて商品をピックアップするため、必要な人手も増え、それに伴って人件費がかさむことになります。このような無駄なコストを減らすためには、カートピッキングを改善し、より効率的な方法に切り替える必要があります。
◇AMRで作業時間削減
カートピッキングに比べ、AMRを導入することで効率が大きく改善されることが分かっています。実際の検証結果では、AMRが人手で行う作業よりも6分36秒速く作業を完了させたという報告もあります。これにより、作業時間の短縮が実現でき、より効率的な作業が可能となります。
AMRを導入すると、作業者の負担が減り、ヒューマンエラーも抑えられます。さらに、作業の効率化により生産性が向上し、企業の評価や信頼を高めることが期待できます。
AMR導入時に検討すべきことは?
AMR(自律走行搬送ロボット)を導入する際には、いくつかの重要な点を検討する必要があります。役割分担の明確化やマニュアル作成はその一部です。また、AMR導入のメリットとデメリットを把握しておくことも大切です。
◇役割分担を明確に
AMRを導入する際、運用を効果的に行い、費用対効果を最大化するためには、役割分担を明確にすることが重要です。具体的には、AMRがどの作業を担当し、人がどの作業を行うのかを明確にしておく必要があります。導入前に作業者と共に役割分担を確認しておくと、スムーズな運用が可能になります。
また、AMRの導入には多くの利点が期待できますが、運行管理が難しいという課題もあります。例えば、AMRが人や障害物にぶつかったり、複数台のAMRが渋滞を引き起こしたりする可能性もあります。これらの問題を防ぐためにも、役割分担の明確化は欠かせません。
◇マニュアルの作成
AMRの導入に際しては、作業マニュアルやトラブルマニュアルを事前に作成しておくことが求められます。ロボットであるAMRは、作業者とは異なり故障やトラブルが発生する可能性があるためです。万が一の事態に備えて、故障やトラブルが発生した場合にどのように対処するかを記載したマニュアルを作成し、作業者全員と共有しておくと安心です。
また、マニュアル作成時には、作業マニュアルだけでなく、AMRの運用が難しくなった場合の対応方法も含めておくことが重要です。これにより、トラブルが発生した際にも冷静に対応でき、作業の中断を防ぐことができます。
仕分けの自動化で作業時間削減
AMR(自律走行搬送ロボット)を導入することで、仕分け作業の自動化が進み、作業時間を大幅に短縮することができます。AMRを導入する前と比べ、作業時間を3分の1に削減できる可能性があります。ここでは、食品スーパー向けの商品を店舗別に仕分ける物流センターでの導入事例を紹介します。
◇店舗別仕分けで導入
この物流センターでは、出荷オーダーに基づき、食品スーパー向けの商品を店舗別に仕分ける作業にAMRが活用されています。導入前、このセンターでは「将来的な競争力を確保するため、省力化と自動化の更なる推進」を課題としていました。
AMRの導入により、店舗別仕分け作業が自動化され、作業の効率化が実現しました。その結果、顧客から高い評価を得るなど、さまざまな良い結果を得ることができました。
◇3分の1に時間削減
AMRを導入する前、この物流センターでは商品仕分けに約3時間を要していました。しかし、AMRによって店舗別仕分け作業が自動化された結果、作業時間を2時間削減することができました。この2時間の削減により、別の作業を行う時間が生まれ、作業の効率化だけでなく、生産性の向上にもつながっています。
AMRの導入によって、業務全体の効率が向上し、より効果的な運用が可能となったと言えるでしょう。
導入時間を90%削減したPallBot
AMR(自律走行搬送ロボット)を導入することで、さまざまな利点が得られます。例えば、物流倉庫や物流センターの省人化、作業の効率化、コスト削減、品質の安定、作業者の負担軽減などが挙げられます。ここでは、AMRの導入時間を90%に削減したPallBotについて詳しく紹介します。
◇導入時間を90%削減したPallBotとは?
AMR(自律走行搬送ロボット)は、誘導体の設置が不要で自動走行が可能という特長があります。この点が、誘導体を必要とするAGV(自動誘導車)との大きな違いであり、AMRの導入には比較的少ない時間での準備が可能です。
特に、大喜産業株式会社が開発した協働型パレタイジングシステム「PallBot」は、導入にかかる時間を90%削減することに成功しています。このように、PallBotは短期間でのAMR導入を実現するため、急速に導入を進めたい企業にとって非常に有力な選択肢となっています。
さらに、PallBotはパレタイジングプログラムの構築が容易であり、用途変更にも迅速に対応できる柔軟性を持っています。例えば、倉庫内でのレイアウト変更や工程変更が頻繁に行われる環境でも、短期間で運用を再開することが可能です。
これにより、企業は業務環境の変化に合わせて柔軟に対応し、効率的な運用を維持することができます。
大喜産業株式会社は、PallBotの開発を通じて、より柔軟で使いやすいソリューションを提供し、価格を抑えつつロボットパレタイザをより身近な存在にしています。このような取り組みにより、ロボットを導入するハードルが下がり、多くの企業にとってアクセスしやすい技術となっています。
AMR(自律走行搬送ロボット)は、物流や製造業で注目されており、従来のカートピッキング作業を効率化するための解決策として活用されています。カートピッキングは作業者が手動で商品をピックアップし移動させるため、長時間の移動や重い荷物の取り扱いで作業者に負担をかけ、効率低下やヒューマンエラーの原因となります。さらに、作業時間の長さや確認作業の多さが人件費の増加にもつながります。
AMRは自動走行が可能で、作業者の負担を軽減し、ヒューマンエラーを減少させるとともに、作業時間を大幅に短縮することができます。実際の事例では、AMRが従来の手作業よりも約6分36秒速く作業を完了させ、作業の効率化が進みました。
AMRを導入する際は、役割分担やマニュアルの整備が重要です。役割分担を明確にし、作業者とロボットの協力体制を構築することで運用がスムーズになります。また、AMRのトラブルや故障に備えたマニュアル作成も不可欠です。
さらに、AMRを活用することで、仕分け作業の自動化が進み、作業時間を大幅に削減できることが実証されています。物流センターでは、AMRによって店舗別仕分け作業が自動化され、作業時間を3分の1に短縮した事例もあります。
また、PallBotというAMRは導入時間を90%削減することに成功し、迅速に運用を開始できる点でも注目されています。このような柔軟で効率的な運用が可能なAMRは、企業にとってコスト削減や作業の効率化に大きく貢献します。
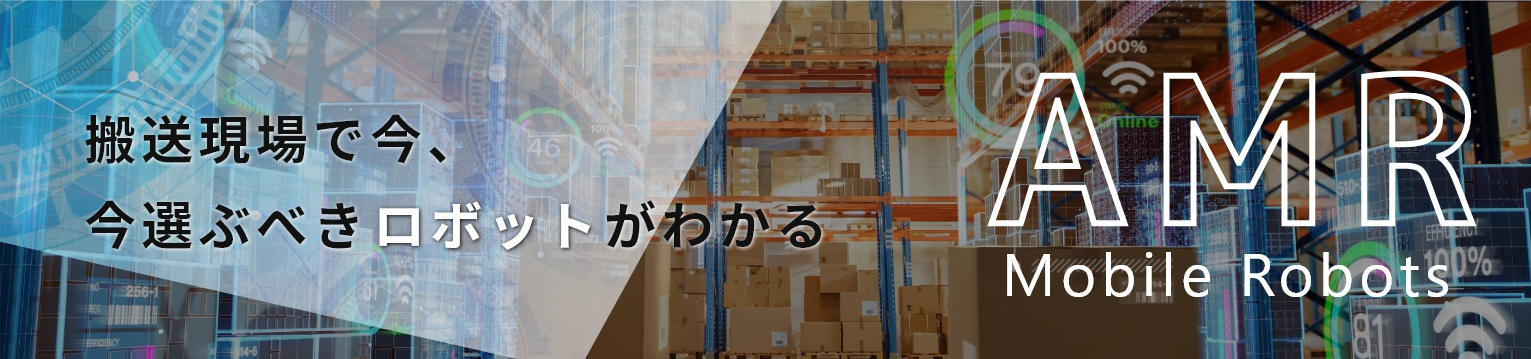