AMRは協働型搬送ロボット!利点や欠点および導入時の注意点とは | 搬送ロボットガイド
AMR
AMRは協働型搬送ロボット!利点や欠点および導入時の注意点とは
公開:2024.02.27 更新:2024.10.07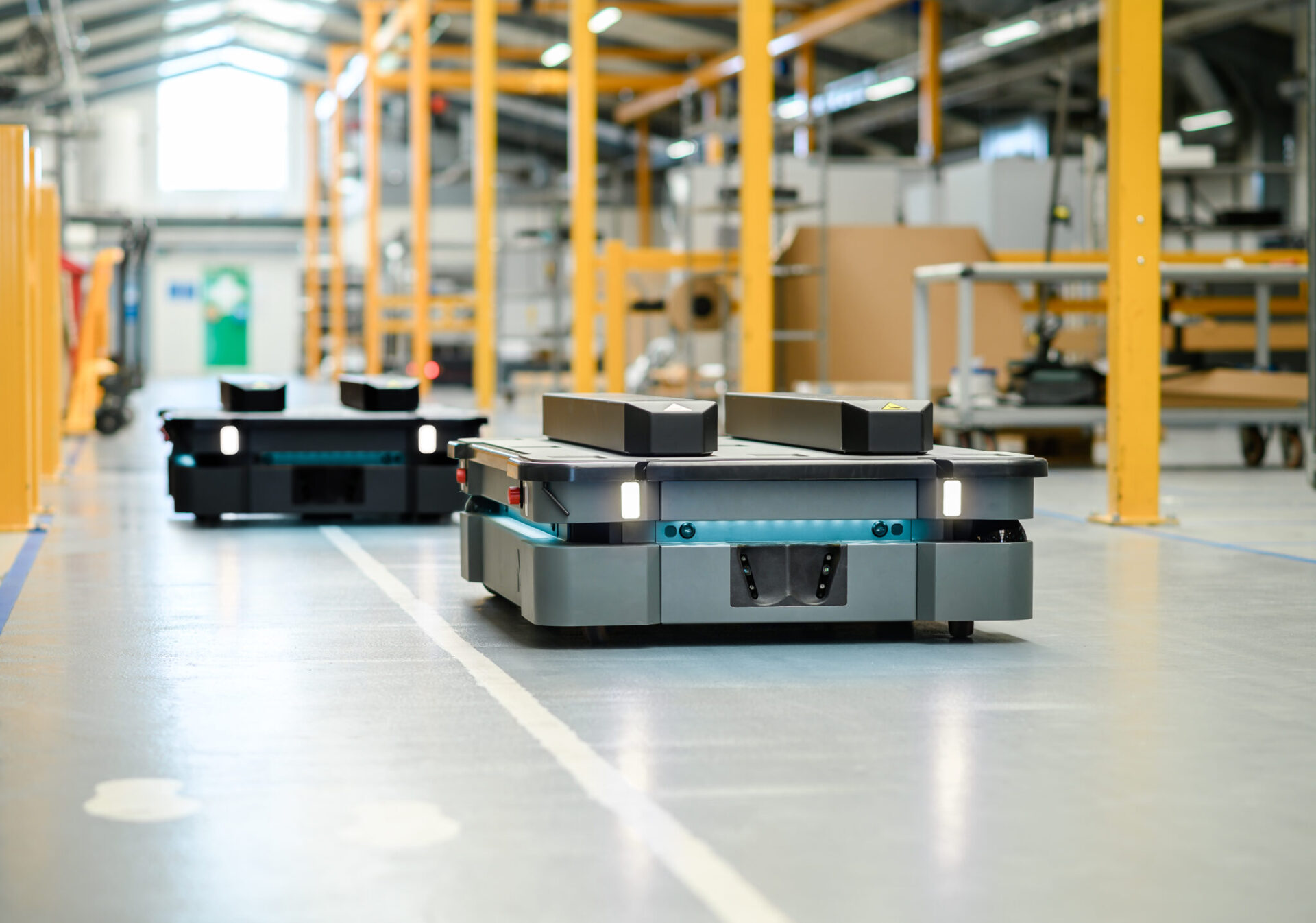
AMRはセンサーを備え、自由に移動できるため、様々な作業現場で協働が可能です。導入期間が短く、設備の変更が不要です。ただし、高額な導入費用や移動スペースの確保が課題です。導入により作業時間短縮や人件費削減のメリットがあり、定期的な改良で競争力向上に貢献するでしょう。慎重な計画と準備が必要です。
目次
AMRは協働型搬送が可能な優れたロボット
決まったルートしか移動できないAGV(無人搬送車)とは異なり、自由自在に移動できるAMR(自律走行搬送ロボット)は、センサーで従業員を感知し回避できるため、人とロボットの協働を実現できます。動作環境の変化に柔軟に対応でき、既存の設備のまま導入できるため、他の産業ロボットに比べ導入に時間がかかりません。
◇人とロボットの協働の実現が可能
荷物を搬送する移動ロボットには、AGV(Automatic Guided Vehicle)とAMR(Autonomous Mobile Robot)の2種類があります。AGV(無人搬送車)は、磁気テープなどを使い搬送経路にラインを敷きAGVをラインに沿って走らせる仕組みのため、決まったルートしか走行できません。一方、AMR(協働型搬送ロボット)は地図の自動作成機能を使って、自由自在に移動します。センサーで従業員を感知し回避できるため、人とロボットの協働の実現が可能です。
◇動作環境が変化しても柔軟に対応可能
倉庫や製造現場では、頻繁に作業員や設備の配置が変わり、それに伴い動作環境やレイアウトも変更されます。搬送ルートを設定しておくAGVは、動作環境の変化に対応できないため、その都度新しいラインを設定します。搬送ルートを算出できるAMRであれば、動作環境の変化に柔軟に対応できるので、稼働現場で支障をきたす心配もありません。
◇既存設備への影響が少なく短期での導入が可能
産業ロボットを導入する際は、設備を入れ替えたり、大規模な工事を行ったりするのが通常です。初期導入費用が高額になるだけでなく、設備の変更や工事をしている間に、業務に影響を及ぼすデメリットもあります。AMRは、既存の設備のまま導入できるため、これまでの業務を続けながら短期間で導入できるのもメリットです。スモールスタートもしやすく、一台からの導入も可能です。
AMR導入で得られる利点と注意すべき欠点
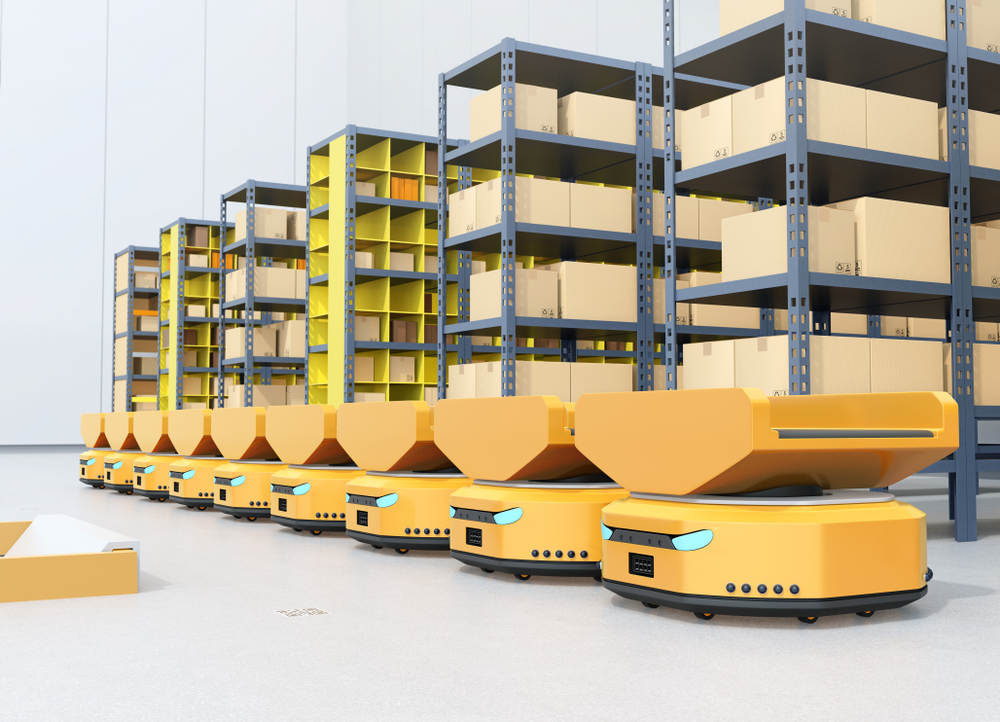
AMRを導入すると、作業時間を短縮し人件費を削減でき、技術教育が必要なくなるメリットもあります。その反面、導入費用とランニングコストがかかり、導入する機種によってはレイアウトチェンジが必要になるのがデメリットです。
◇作業時間と人件費の削減
ピッキング作業のほとんどは、移動時間に使われているといわれています。AMRは、地図の自動作成機能を使って最短ルートを探索し、効率よく荷物を搬送できるロボットです。AMRの導入による最大のメリットは、搬送作業をAMRに搬送を任せることで、作業員が移動する必要がなくなり、作業時間を短縮できる点です。作業員の作業量も削減できるため、作業員を減らし人件費の削減も可能です。
◇スタッフの技術教育が不要になる
物流現場に新人スタッフが加わると、作業を始める前にスタッフの技術教育が必要です。技術を教えて慣れるまでに時間がかかり、一人前になっても辞めてしまえば、また新しいスタッフに技術教育をしなくてはいけません。AMRは導入すれば故障するまで使えるため、スタッフの技術教育が不要になります。
◇導入費用とランニングコストの確保が課題
AMRはAGVよりも導入しやすい反面、本体価格が高く1台あたり数百万から数千万円します。300万円のAMRを10台導入するとそれだけで3,000万円、システム導入費用、移動式カート、自動充電器、運用管理システムなども必要です。さらに、ランニングコストとして、電気代、メンテナンス費用なども必要なため、導入する際は資金の確保が課題です。
◇ロボットの移動スペースの確保が必要
既存設備を活用できるAMRですが、ロボットが移動するためのスペースは確保しなくてはいけません。機種によっては幅が1m以上あるため、移動スペースが狭い場合はレイアウトチェンジが必要です。
協働型搬送ロボットのAMR導入での注意
AMRを安全に運用し導入効果を得るためには、いくつかの注意点があります。導入前にしておくべきことは、作業フローとトラブル時の対応方法の明確化、本体サイズの確認で、導入後の導入効果の検証と定期的な改良も重要です。
◇作業フローを明確化しサイズを確認
作業現場では、AMRとスタッフが分業します。しかし、荷物の搬送はAMR、それ以外の作業はフタッフというような大まかな作業の振り分けでは、AMRが搬送している間スタッフが無駄に待機する可能性があります。AMRを導入して業務の効率化を図るためには、AMRとスタッフが効率よく協働できるように、作業フローを明確にしておくことが大切です。また、通路の幅が狭いとAMRが迂回をして搬送に時間がかかってしまうため、本体のサイズも確認し通路の確保もしておきましょう。
◇トラブル発生時の対応方法
AMRは人との協働が可能ですが、事故が起こらないというわけではありません。実際に、スタッフとAMRの接触事故が発生しているため、トラブル発生時に備えて対処方法を検討しておくことが重要です。AMRは本体の故障やシステム不具合によって止まってしまうこともあるため、トラブル発生時の対処方法を記載したマニュアルを作成し、スタッフ全員に周知しておくことも大事です。
◇導入効果の検証と定期的な改良
AMRを導入したにもかかわらず、業務効率化や経費削減にそれほど効果が現れないこともあります。その主な理由は、可動範囲、台数、レイアウトなどです。AMRを効果的に運用するためには、導入効果の検証を行い定期的な改良を行う必要があります。検証と改良を行う手順は、定量的・定性的な分析と課題の洗い出し、改善策の実装、モニタリングです。作業フローやレイアウトも定期的に見直すと、AMRの効果的な運用を実現し、業務効率の持続的な向上を図れます。
AMR(自律走行搬送ロボット)は、従業員を感知し回避できるセンサーを備え、AGV(無人搬送車)と比較して自由自在に移動できるため、倉庫や製造現場など様々な作業環境での人とロボットの協働を可能にします。
特に、作業現場では動作環境や作業フローが頻繁に変化するため、従来のAGVでは対応が難しかった課題をAMRが解決します。AMRは地図の自動作成機能を活用して、新しい環境にも柔軟に適応し、作業効率を向上させます。
また、AMRは既存の設備のまま導入できるため、大規模な設備の改修や工事を必要とせず、導入期間が短縮されます。
一方で、AMRを導入する際にはいくつかの課題も存在します。導入費用やランニングコストが高額であり、また、AMRが移動するためのスペース確保やレイアウト変更が必要な場合があります。
さらに、トラブル発生時の対応や導入後の効果検証、定期的な改良など、運用面でも様々な課題が生じます。
それにもかかわらず、AMRを導入することで多くの利点が得られます。例えば、作業時間の短縮や人件費の削減、作業員の技術教育が不要となることで、業務効率の向上やコストの削減が期待できます。また、AMRは導入後も定期的な改良や最適化が可能であり、長期的な視野での利益をもたらします。
したがって、AMRを導入する際には慎重な計画と適切な準備が必要です。作業フローの明確化やトラブル対応策の整備、効果検証と改良のサイクルの確立など、綿密な計画が成功の鍵となります。
AMRは技術の進化と共にさらなる進化が期待される分野であり、適切な導入と運用によって企業の競争力向上に大きく寄与するでしょう。
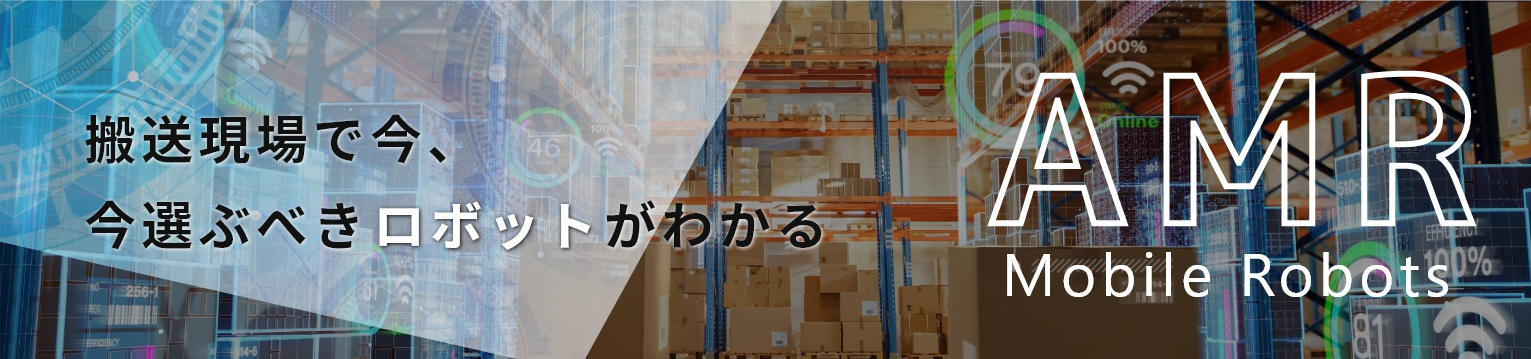