ピッキングアシストAMRとは?生産性を改善させた導入事例 | 搬送ロボットガイド
AMR
ピッキングアシストAMRとは?生産性を改善させた導入事例
公開:2024.07.24 更新:2025.07.29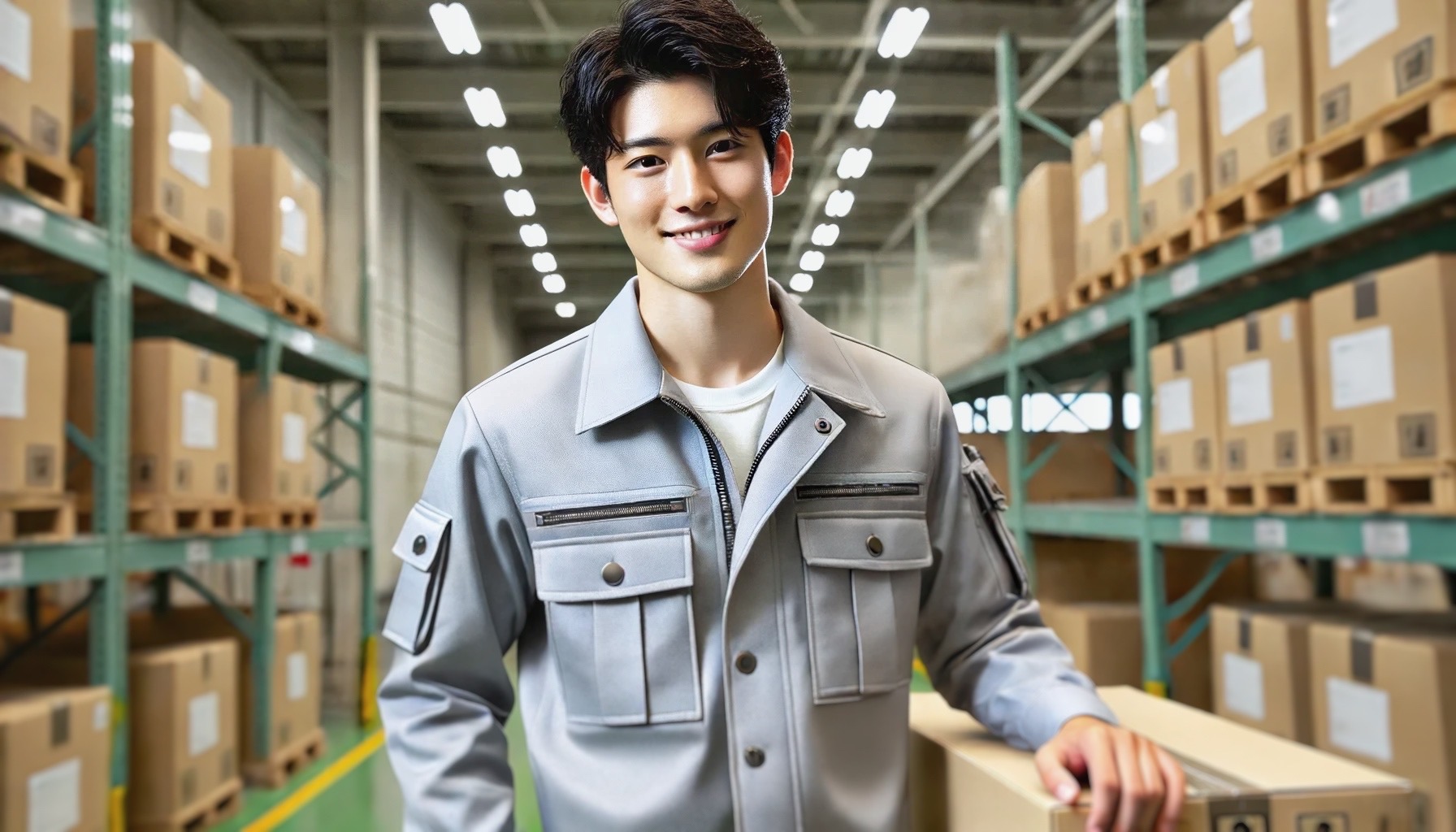
AMR(自律移動ロボット)は、倉庫内で自律的に移動しピッキング作業を行うロボットです。センサーとAI技術で最適ルートを計算し、効率的に作業を進めます。24時間稼働し倉庫の稼働率を最大化、誤配送や遅延を防ぎます。しかし、高い初期コストやインフラ統合の難しさ、技術サポートと従業員のトレーニングが課題です。実際にロジスティクス千葉第1センターやロジスティード東日本で生産性向上とミス削減が実現されています。
目次
倉庫でのピッキングに役立つAMRとは?
AMRは倉庫内で自律的に移動しピッキング作業を行うロボットで、センサーとAIで効率を向上させ、24時間稼働します。しかし、初期コストやインフラ統合、サポート体制の整備が課題です。
◇AMRとは
AMR(Autonomous Mobile Robot、自律走行搬送ロボット)は、物流倉庫や工場などで活躍する次世代のロボットです。従来のAGV(無人搬送車)と異なり、AMRはセンサーやAI技術を駆使して周囲の環境をリアルタイムで認識し、地図を自ら作成しながら最適なルートを自律的に選択して移動します。
ピッキングや搬送など指定された作業を自動でこなすだけでなく、作業員や障害物がルート上に現れた場合でも減速や回避を行い、人と協働しながら柔軟に作業できるのが大きな特徴です。これにより、作業員の移動距離や負担が大幅に軽減され、倉庫全体の効率化や生産性向上に大きく貢献しています。
・AGVとの違い
AGVはあらかじめ設置された磁気テープや誘導体などのガイドに沿って決められたルートを走行するのに対し、AMRはガイドレスで自由に現場を移動できます。環境の変化や障害物に対しても、その場で最適なルートに再計算し、柔軟に対応できるため、レイアウト変更や運用改善にも迅速に対応可能です。
・技術的な仕組み
AMRはLiDARやカメラ、各種センサーを搭載し、SLAM(Simultaneous Localization and Mapping)技術で自己位置推定と周囲の地図作成を同時に行います。AIによる経路探索や障害物回避アルゴリズムを活用し、リアルタイムで最適な経路を自動算出。無線通信で上位システムと連携し、作業指示や進捗管理も自動化されています。
◇AMR導入のメリット
AMRの導入には、以下のような多くのメリットがあります。
・作業効率の大幅向上
人手によるピッキングや搬送作業の自動化により、作業員の移動距離や負担を削減。24時間稼働も可能で、倉庫や工場の稼働率を最大化できます。
・柔軟な運用
ガイドレスでレイアウト変更にも即応でき、新しい作業フローやゾーンの追加にも柔軟に対応します。
・安全性の向上
人や障害物を自動で検知・回避し、事故や衝突リスクを低減。人とロボットが同じ空間で安全に協働可能です。
・リアルタイム最適化
稼働データの収集・分析により、誤配送や遅延の防止、在庫管理や工程管理の最適化も実現します。
◇AMRの課題と導入時の注意点
一方で、AMR導入にはいくつかの課題も存在します。
・初期導入コストの高さ
AMRは高度なセンサーやAI技術を搭載しているため、購入や設置に多額の初期投資が必要です。中小企業にとっては大きな負担となる場合があり、費用対効果の見極めが重要です。
・既存インフラとの統合の難しさ
AMRはガイドレスで柔軟な運用が可能ですが、既存の倉庫レイアウトや運用プロセスとの統合には調整が必要です。場合によっては倉庫内のゾーニングや作業フローを見直す必要があり、導入前の現場調査やシミュレーションが不可欠です。
・技術的なサポート体制の必要性
AMRの運用には、障害発生時やトラブル時に迅速に対応できる技術サポートが不可欠です。メーカーやSIerとの連携体制、保守契約の整備が求められます。
・従業員のトレーニング
AMRを効果的に活用するためには、現場スタッフのトレーニングも重要です。操作方法や管理手順、トラブルシューティングの知識を習得し、現場での運用に慣れるまでには一定の教育期間が必要となります。
◇AMRの今後と展望
物流や製造現場の人手不足・高齢化、EC市場の拡大による業務量増加などを背景に、AMRの需要は今後ますます高まると予想されています。AIやロボティクス技術の進化により、AMRの導入コストは徐々に低下し、より多機能・高性能なモデルも登場しています。
また、AMR同士の協調制御や、WMS(倉庫管理システム)・MES(製造実行システム)など上位システムとの連携も進み、現場全体の自動化・最適化が加速しています。今後は、より多様な現場や中小規模の倉庫にもAMRが普及し、物流・製造業の生産性向上や働き方改革に大きく貢献することが期待されています。
AMRは、AIとセンサー技術による自律走行能力で、従来のAGVとは一線を画す次世代の搬送ロボットです。人と協働しながら柔軟に作業できる点や、ガイドレスでレイアウト変更にも即応できる点が大きな魅力です。一方で、導入コストや運用体制、従業員教育などの課題もあるため、現場の状況や将来の運用計画を踏まえた慎重な導入検討が重要です。
今後もAMRは、物流・製造現場の自動化と効率化をけん引する存在として、さらなる進化と普及が期待されます。
【あわせて読みたい】
▼物流の自動化を加速するアイオイ・システムのデジタルピッキングとは?
ロジスティクス千葉第1センターの導入例
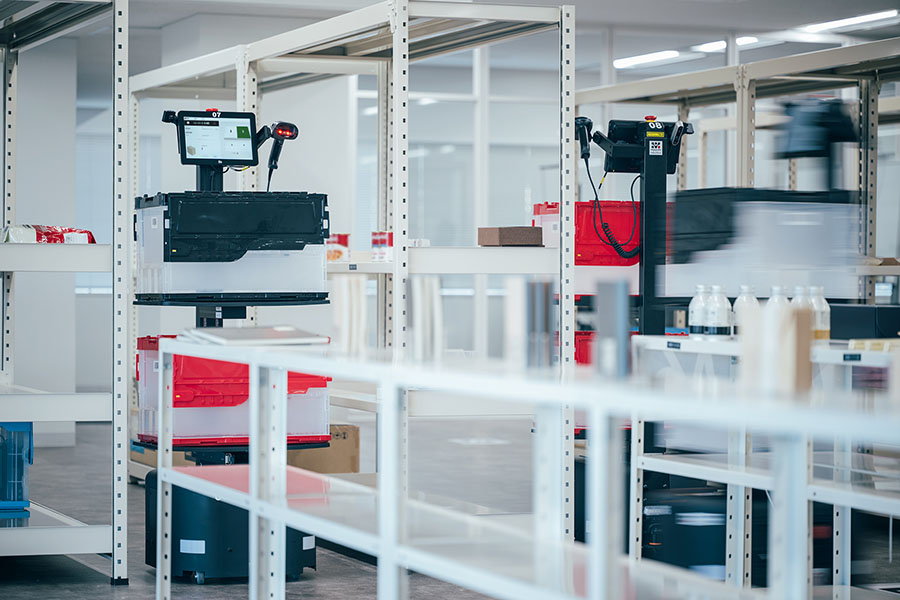
物流現場の人手不足や業務効率化は、今や多くの企業にとって喫緊の課題です。特にEC市場の拡大や多品種・多品目化が進む中、従来の人手作業だけでは高い生産性とサービス品質の維持が難しくなっています。
こうした背景のもと、株式会社Rise UP(ライズアップ)は、ラピュタロボティクスの協働型ピッキングアシストロボット「ラピュタPA-AMR」を2024年、千葉県の物流センターに15台導入し、既存のカートピッキングと共存させる形で現場改革を進めています。
◇導入の背景
Rise UPは、主にコンタクトレンズの通販・卸を手がける企業で、千葉の物流センターでは常時4万SKU(品目・ロット)を管理しています。従来はWMS(倉庫管理システム)とハンディターミナルを活用し、人手によるマルチカートピッキングを行っていました。
しかし、品目の増加とともに作業の複雑化・負荷増大が進み、加えて慢性的な人材確保難が深刻化。安定した事業継続やサービス品質維持のため、生産性と効率性の抜本的な向上が求められていました。
◇ラピュタPA-AMR導入の決め手と評価ポイント
Rise UPがラピュタロボティクスの「ラピュタPA-AMR」を選定した理由は、いくつかの明確な強みがあったからです。
・既存運用との共存が容易
ラピュタPA-AMRは、既存のカートピッキングを止めることなく、現場の運用を大きく変えずに導入できる点が大きな魅力でした。現場のオペレーションを維持しつつ、段階的にロボット活用を拡大できるため、現場への負担や混乱を最小限に抑えることが可能です。
・実績に裏打ちされた開発力
ラピュタロボティクスは国内外の物流現場で多くのAMR導入実績を持ち、現場で生まれる課題を迅速にフィードバックし、独自のロジックや機能開発に活かしてきました。こうした現場密着型の開発姿勢と、クラウドロボティクスプラットフォームによる高い拡張性・柔軟性も評価されました。
・シンプルな操作性と現場への馴染みやすさ
ピッキング作業者にとって操作が簡単で、違和感なく現場に馴染むことができた点も高く評価されています。新しいテクノロジー導入時に課題となる「現場の抵抗感」が少なく、現場スタッフからも好意的な反応が得られました。
◇ラピュタPA-AMRの活用ポイント
・カートピッキングとAMRのハイブリッド運用
Rise UPでは、従来のカートピッキングとラピュタPA-AMRによるピッキングを併用しています。物流の波動や繁忙期・閑散期に合わせて両者のバランスを調整し、現場全体の生産性・効率性を最大化。AMRが単独で稼働するのではなく、人とロボットが協働することで、より高いサービスレベルを維持しています。
・Put to Light機能による誤ピッキング防止
ラピュタPA-AMRのトレーにはLEDが搭載されており、ピッキングした商品をどのコンテナに格納するかを明確に指示します。これにより作業者は迷わず正確にピッキングでき、誤ピッキングを未然に防止。作業の視認性も大きく向上し、品質管理と生産性向上の両立を実現しています。
・作業習得の早期化と現場の働きやすさ向上
AMRの導入により、作業が単純化され、未経験者でも短期間でピッキング作業を習得できるようになりました。体力的な負担も軽減され、ワークライフバランスの向上や、より良い職場環境づくりにも貢献しています。
◇現場の声と導入効果
Rise UPのロジスティクス本部 部長 執行役員・西原良和氏は「現在は増台も検討するほど、AMRはピッキング作業のパートナーになっている」と語ります。また、AMRのソフトウェアアップデートも定期的に行われ、現場とともに進化している実感があるとしています。
改善グループの竹下佳輝氏も「現状の運用を止めずに導入できたことが決め手。生産性向上だけでなく、作業の単純化による習得の早期化など、多くの効果があった」と評価。今後はピッキング工程だけでなく、補充や入荷など他の用途にもAMR活用の幅を広げ、さらなる現場改善を目指しています。
Rise UPは、今後もラピュタPA-AMRの台数増加や新たな工程への活用を検討し、物流現場の生産性向上と働きやすい職場づくりを推進していく方針です。ラピュタロボティクスも、クラウドロボティクスプラットフォームの進化や現場フィードバックを活かし、より高度な協働型ロボットソリューションの提供を続けています。
ラピュタロボティクスは、チューリッヒ工科大学発のベンチャー企業として、世界30カ国以上のエンジニアが集うグローバルな開発体制と、最先端のAI・制御技術を強みに持ちます。日本国内外の多様な現場で培ったノウハウを活かし、ユーザーごとに最適なロボット導入・運用支援を提供しています。
Rise UPの物流センターにおけるラピュタPA-AMR導入事例は、多品種・多品目化が進む現代物流において、人とロボットの協働による現場改革の好例です。既存運用との共存、誤ピッキング防止機能、作業習得の早期化など、現場の課題に即した機能と運用ノウハウが高く評価されています。今後もAMRの進化と普及が進む中、ラピュタロボティクスとRise UPの取り組みは、物流現場の未来を切り拓くモデルケースとして注目されるでしょう。
【あわせて読みたい】
▼AMR導入によるピッキング作業の効果とは?生産性の向上に貢献
大型の箱も扱えるピッキングロボット
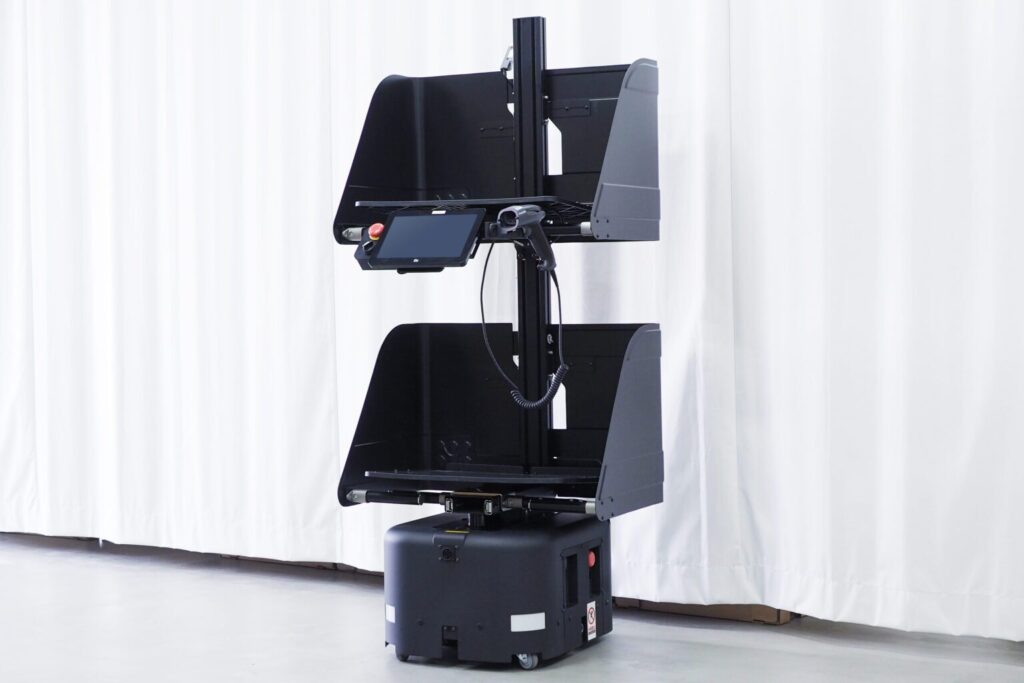
ロジスティード東日本の「柏の葉営業所」は、ピッキングロボット導入で労働生産性を大幅に改善しました。ロボットは高速かつ正確に商品を取り扱い、大型の箱にも対応できるため、作業員の負担軽減とミスの減少が実現しています。
◇労働生産性を改善
ロジスティード東日本の「柏の葉営業所」では、ピッキングロボットの導入により、物流センターでは労働生産性が大幅に改善されました。従来の手動ピッキング作業に比べて、ロボットは高速かつ正確に商品を取り扱うことができます。
ロボットによりピッキング作業を導入することで、作業員の負担が軽減され、ミスが減少します。
◇大型の箱にも対応
大型の箱を扱えるピッキングロボットは、重量物や大きなサイズの荷物に対応する能力が高く、物流センターでの汎用性が優れています。
ロボットは、安定した持ち上げ能力と精密な位置決め機能を備えており、重量のある荷物を安全に持ち上げ、指定された場所に正確に配置することができます。
このため、大型商品の取り扱いが必要な業務でもスムーズに運用することが可能です。
コクヨサプライロジスティクスの導入例
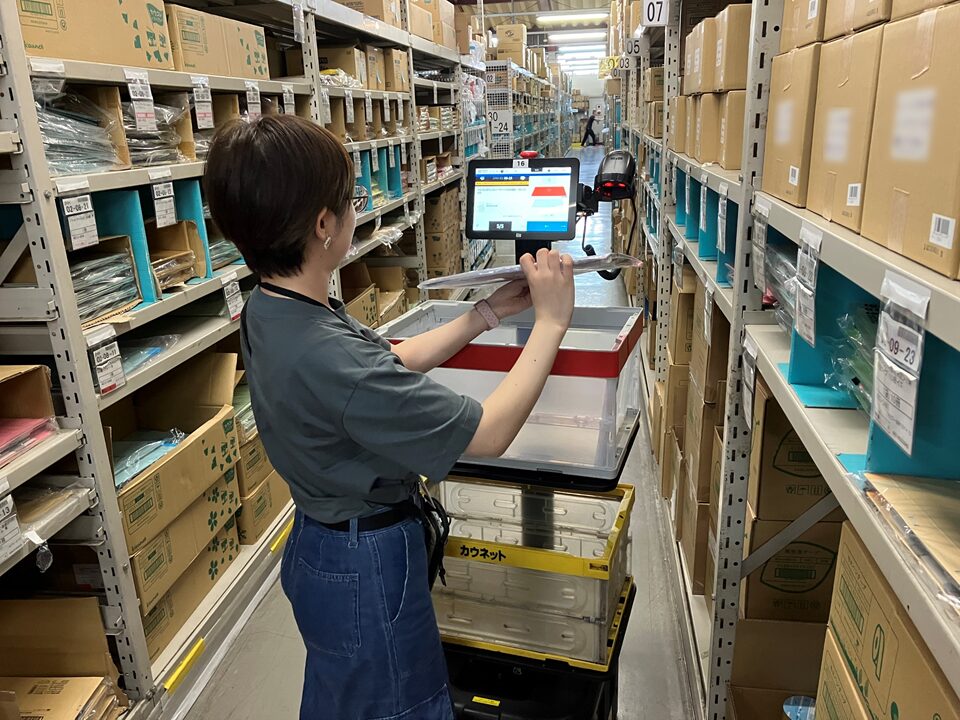
コクヨサプライロジスティクスは、最新の自動化技術を取り入れ、物流業務の効率化と省人化を推進しています。最新の自動化技術を取り入れる取り組みにより、作業の迅速化とコスト削減が実現されました。
◇自動化と省人化を目指す
コクヨサプライロジスティクスは、物流業務の自動化と省人化を目指して先進的な技術を導入しています。自動ピッキングシステムや自律移動ロボット(AMR)を取り入れ、倉庫内の作業を自動化し、効率化を図っています。この自動化により、従業員の手作業が大幅に削減され、作業の精度も向上しました。
また、省人化によって人件費の削減が可能となり、企業の競争力が高まります。特に、AIを活用したシステムはリアルタイムでデータを分析し、最適な作業手順を提示することで、従業員の負担を軽減しながら生産性を向上させています。
◇歩行時間が減少
コクヨサプライロジスティクスの自動化技術導入により、倉庫内での歩行時間が大幅に減少しました。
従来、作業員は広大な倉庫内を長時間歩き回りながらピッキング作業を行っていましたが、AMRの導入により作業の自動化が進み、作業員の移動距離が短縮されました。これにより、作業効率が向上し、全体の作業時間が短縮されました。
さらに、自動ピッキングシステムは商品の位置を正確に把握し、最適なルートでピッキングを行います。これによりミスが減少し、作業のスピードも向上しました。作業スピードの向上により、従業員は疲労が軽減され、安全に作業を行えるようになります。
【あわせて読みたい】
▼物流現場で不可欠なピッキングカート!効率化の鍵はAMRの活用?
AMRの導入を検討するならおすすめメーカー3選
◇大喜産業株式会社
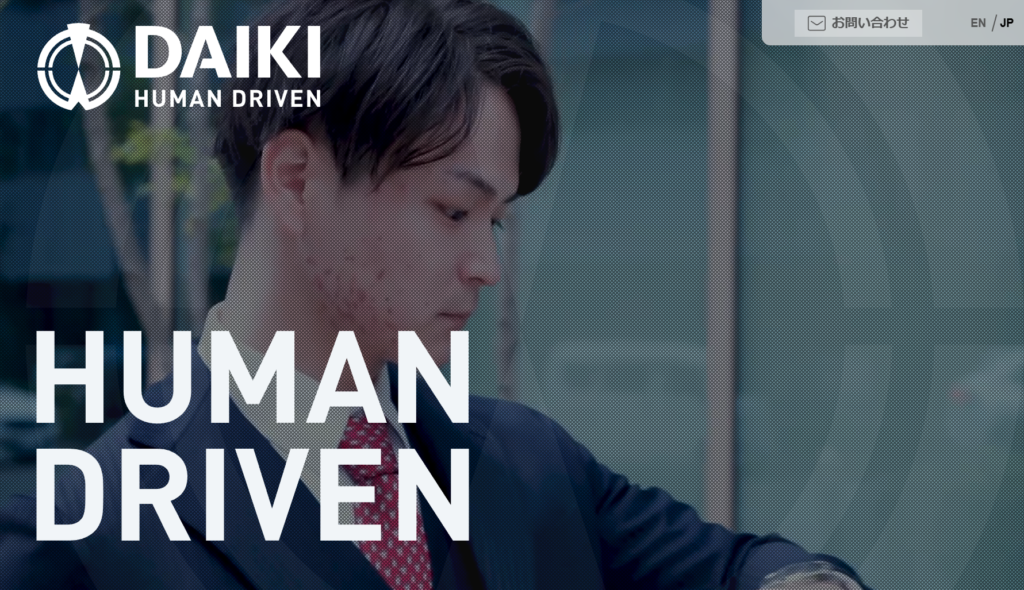
大喜産業株式会社は、大阪市西区に本社を構える老舗企業で、産業用ロボットおよび自動化ソリューション分野で高い実績を誇ります。「和合」「実行」「今を活かす」「感謝」「自信」を経営理念に掲げ、持続可能な社会の実現と顧客・社会への貢献を目指しています。
同社の強みは、人と共存できる協働ロボットや自律移動型ロボット(AMR)など、最先端のロボットソリューションの提案力。OnRobot社の自動化プラットフォーム「D:PLOY」搭載のパレタイズロボットや、MiR・ROEQ・TM Robot・ユニバーサルロボットなど世界的メーカーのロボットを幅広く取り扱い、現場ごとの最適な自動化を実現しています。
会社名 | 大喜産業株式会社 |
営業本部 | <住所> 〒550-0012 大阪府大阪市西区立売堀1-5-9 <電話番号> 06-6541-1987 |
営業本部東京オフィス | <住所> 〒100-0004 東京都千代田区大手町1-5-1 大手町ファーストスクエア4F <電話番号> 03-5219-1463 |
大阪支店 | <住所> 〒550-0012 大阪府大阪市西区立売堀1-5-9 <電話番号> 06-6532-0751 |
東京支店 | <住所> 〒333-0815 埼玉県川口市北原台3-2-21 <電話番号> 048-297-1388 |
東京支店つくばオフィス | <住所> 〒305-0031 茨城県つくば市吾妻1-5-7 ダイワロイネットホテルつくば2F <電話番号> 029-817-4844 |
名古屋支店 | <住所> 〒452-0805 愛知県名古屋市西区市場木町416 <電話番号> 052-505-8201 |
東大阪支店 | <住所> 〒581-0861 大阪府八尾市東町4-1 <電話番号> 072-997-0123 |
京滋支店 | <住所> 〒520-3047 滋賀県栗東市手原3-2-3 <電話番号> 077-553-6155 |
四国支店 | <住所> 〒761-0301 香川県高松市林町2554-1 <電話番号> 087-868-4511 |
九州支店 | <住所> 〒812-0895 福岡県福岡市博多区竹下2-4-7 <電話番号> 092-441-0198 |
営業時間 | 公式サイトに記載なし |
公式ホームページ | https://www.daiki-sangyo.co.jp/ |
また、日本ロボットシステムインテグレータ協会など多くの業界団体にも加盟し、80年以上にわたる経験とノウハウを活かして、顧客の生産性向上や人手不足解消に貢献しています。誠実な企業姿勢と技術力で、産業界の進化を支える存在です。
大喜産業株式会社について詳しく知りたい方はこちらも併せてご覧ください。
▼MiR社の魅力的なMiR製品とその販売代理店・大喜産業とは
さらに詳しい情報は公式ホームページでも確認できます。ぜひチェックしてみてください。
◇オムロン株式会社
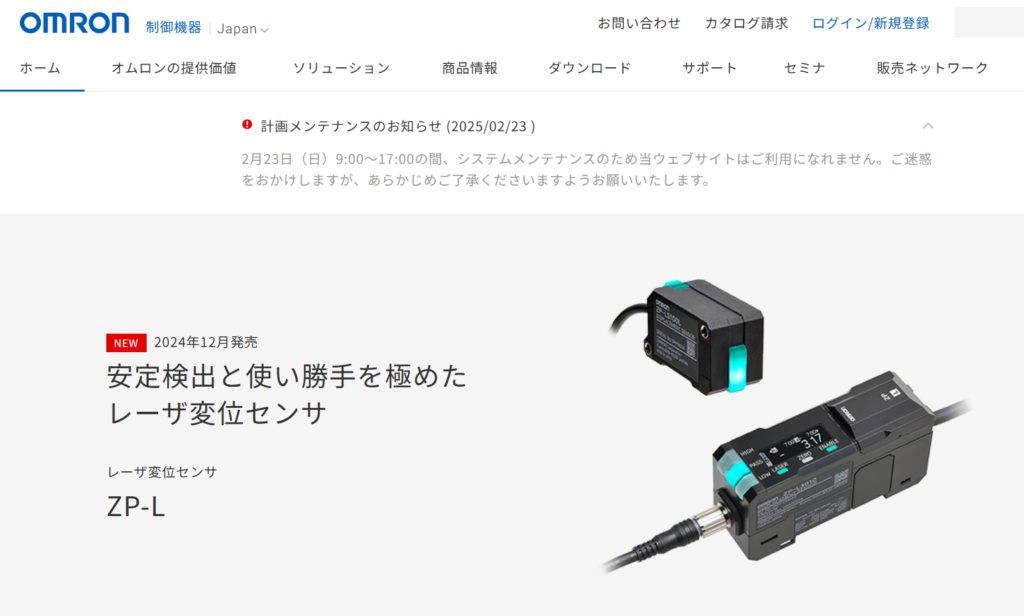
オムロンのモバイルロボット(LD/MD/HDシリーズ)は、世界最多の導入実績を誇る自動搬送ロボットとして、製造業をはじめ多様な業界で活用されています。最大の特長は「高い適応力」と「拡張性」で、搬送・配達・周回など単純作業を自動化することで、人手不足や人件費高騰といった現場課題の解決に貢献します。
またオムロン独自のフリート管理システム「OMRON Fleet Operations Workspace(FLOW)」は、複数台のロボットの位置・作業状況・交通の流れをリアルタイムで最適化。MESやERPなどの上位システムとも連携し、作業指示や優先順位、最短ルート選択、障害物回避、充電スケジュール管理まで一元化できます。
会社名 | オムロン株式会社 |
所在地 | 〒600-8530 京都府京都市下京区塩小路通堀川東入 オムロン京都センタービル |
電話番号 | 075-344-7000 |
営業時間 | 公式サイトに記載なし |
公式ホームページ | https://www.fa.omron.co.jp/ |
ナビゲーション技術も業界最高水準で、マグネットテープやビーコンなどの工事が不要。設置後すぐに稼働でき、ITシステムとの接続やソフトウェアの自動更新も容易です。
オムロン株式会社について詳しく知りたい方はこちらも併せてご覧ください。
▼オムロン「LD-250」の特徴とは?製造業の課題に技術で立ち向かう
◇アルテック株式会社
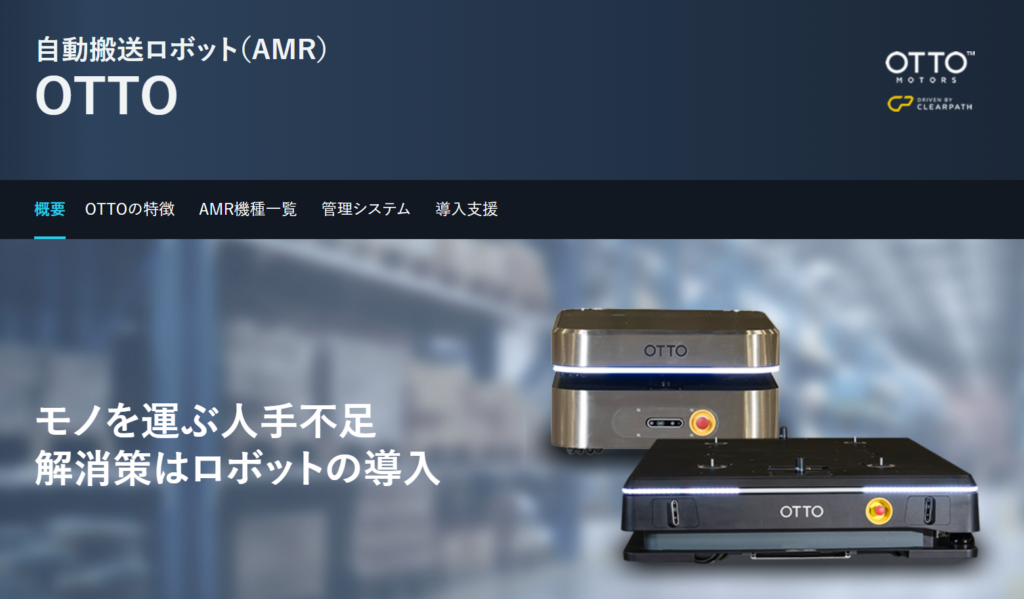
アルテック株式会社は、物流・製造現場の自動化・省人化を支援するソリューションプロバイダーです。近年深刻化する労働力不足や業務効率化の課題に対し、先進的なサービスロボットや自動化システムを提案しています。
主力分野の一つである自律走行型搬送ロボットでは、Clearpath Robotics社のOTTOシリーズ(最大積載量100kg~1,900kg)を取り扱い、SLAM技術によりフロアレイアウトの変更や障害物をリアルタイムで検知し、最適ルートで荷物搬送を自動化します。
会社名 | アルテック株式会社 |
所在地 | 〒104-0042 東京都中央区入船2-1-1 住友入船ビル2F |
電話番号 | 03-5542-6760 |
営業時間 | 公式サイトに記載なし |
公式ホームページ | https://smart-logistics.altech.jp/amr/otto/ |
アルテックは、最先端のロボティクスと自動化技術で、物流現場の最適化とスマート化を強力にサポートしています。
アルテック株式会社について詳しく知りたい方はこちらも併せてご覧ください。
▼OTTO MotorsのAMRの特徴と可能性!日本での普及が期待される理由
まとめ
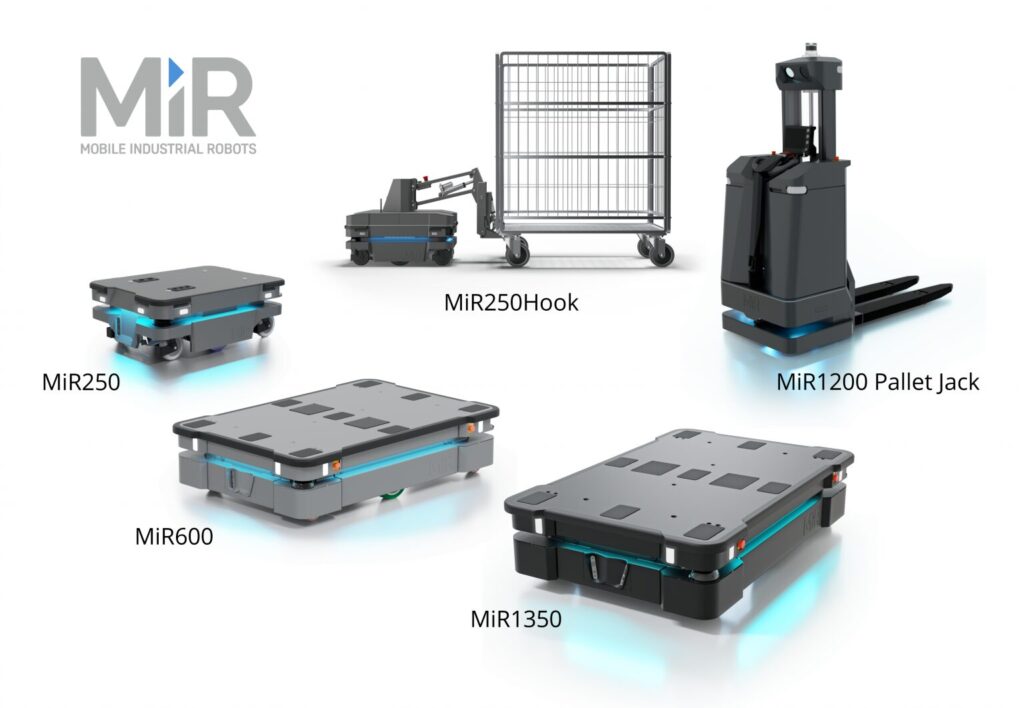
AMR(自律移動ロボット)は、倉庫内で自律的に移動しピッキング作業を行うロボットです。センサーとAI技術を駆使して環境を認識し、最適なルートで効率よく移動します。これにより作業員の移動距離が減り、作業の効率が大幅に向上します。
また、24時間稼働が可能で、倉庫の稼働率を最大化し、誤配送や遅延を防ぎます。
しかし、初期導入コストが高く、既存のインフラとの統合が難しいため、中小企業には大きな負担が伴います。さらに、運用には技術サポートや従業員のトレーニングが必要です。
ロジスティクス千葉第1センターやロジスティード東日本の例では、AMR導入により生産性が向上し、ピッキングミスが減少しました。特に大型の箱にも対応できるロボットは、重量物の取り扱いに優れています。
この記事を読んでいる人におすすめ
▼2024年問題や人手不足に対応!RGVを活用した搬送効率化のポイント
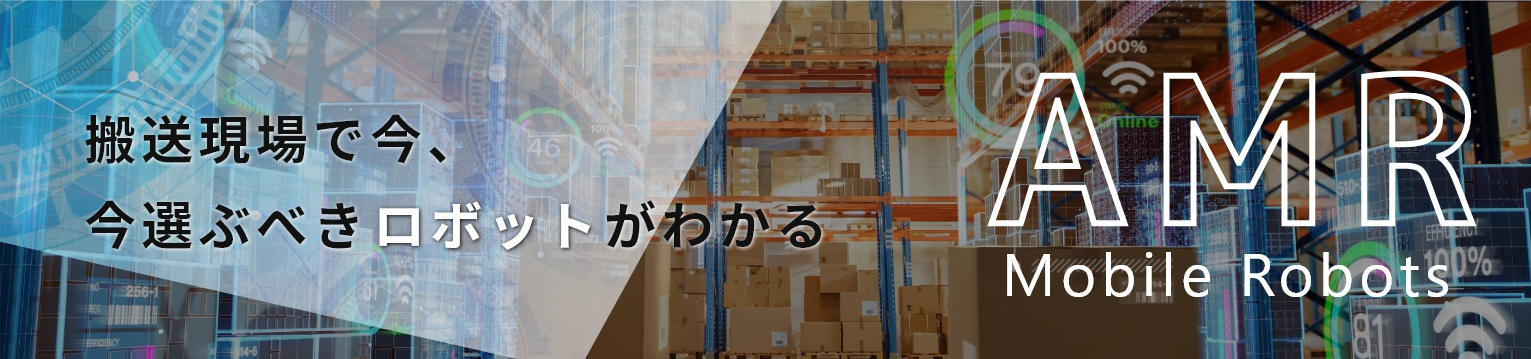