AMR導入によるピッキング作業の効果とは?生産性の向上に貢献 | 搬送ロボットガイド
AMR
AMR導入によるピッキング作業の効果とは?生産性の向上に貢献
公開:2024.04.24 更新:2024.10.07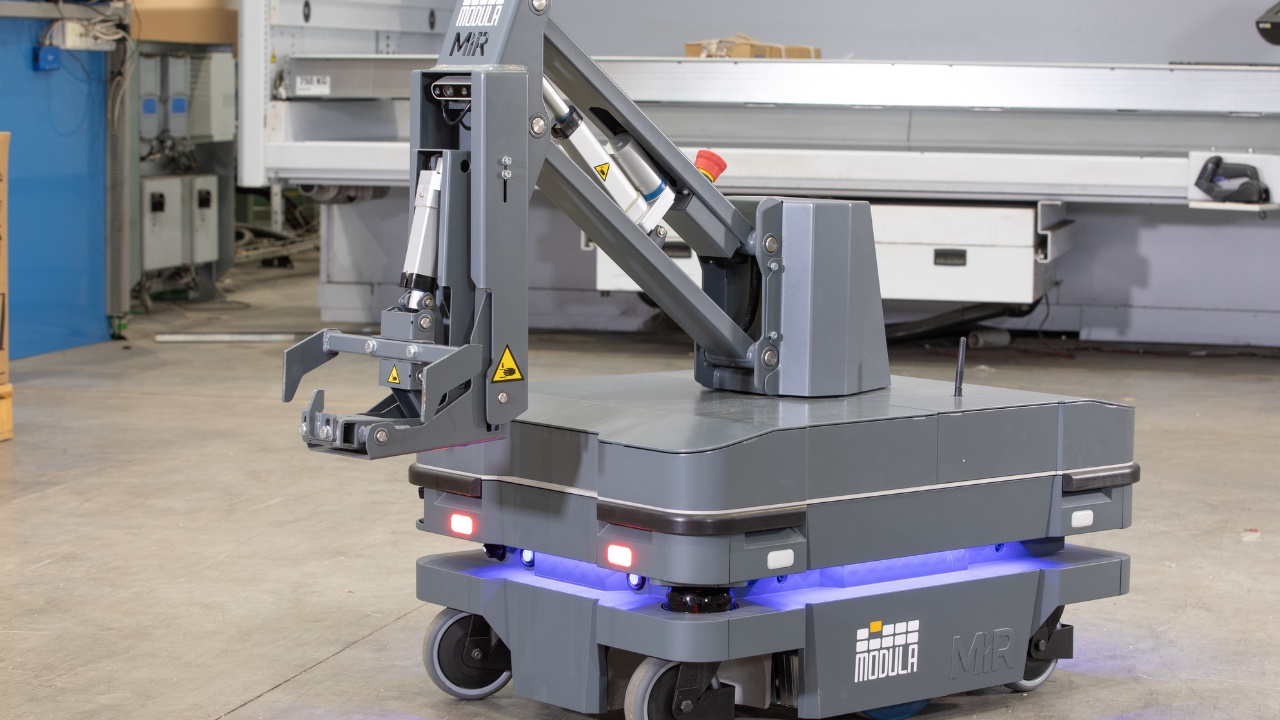
ピッキング作業は倉庫や工場での商品取り出しプロセスで、シングルピッキングでは個別に、トータルピッキングでは複数の注文を処理します。人間が行う場合は疲労や単調さが課題ですが、自動ガイドロボット(AMR)導入で作業効率が向上し、ミスが減ります。AMRは作業時間を短縮し、生産性を高めることが期待されます。
目次
目的の品物を集めるピッキング作業とは?
ピッキング作業は、商品を取り出す重要な作業で、シングルピッキングでは一人が一つずつ商品を取り出し、トータルピッキングでは複数の注文をまとめて取り出す方法です。マルチオーダーピッキングは、複数の注文を同時に取り出し、効率が高いがミスが起こりやすいです。
◇ピッキング作業とは
ピッキングは、工場や倉庫で商品を取り出す作業のことです。
例えば、インターネット通販などで注文した商品を倉庫で見つけ出し、棚から取り出すのがその役割です。多くの商品の中から注文された商品を見つけるため、効率的なピッキングが重要となります。
迅速なピッキング作業により商品を顧客の元に素早く届けることができ、注文の増加や処理の向上につながります。特に通販業界では、企業や店舗の成長に欠かせない要素となっています。
◇シングルピッキング
シングルピッキングは、最も基本となるピッキング方法で、出荷数が少ない工場や倉庫、店舗で採用されています。
このピッキング方法は、作業担当者が担当した注文の商品を棚からひとつずつピッキングして集める方法で、シンプルな反面、一人の担当者がその注文に対して一人でピッキングを行うため、移動が多いことから負担も多く、作業効率が低くなります。
◇トータルピッキング
トータルピッキングは、複数の注文を一括してピッキングし、後でそれぞれの注文に仕分ける方法です。この仕分けの手法から、「種まき方式」とも呼ばれます。
このピッキング方法は、商品の種類が多い場合には適していませんが、商品数が少なく、出荷する商品数が多い場合には有効です。作業員の負担はシングルピッキングよりも軽減されますが、仕分ける場所や作業員が必要となるため、場合によっては作業時間が長くなることがあります。
◇マルチオーダーピッキング
マルチオーダーピッキングは、複数の注文をピッキングして、その場で仕分けるピッキング方法です。
トータルピッキングと異なり、すべての商品をピッキングした後に仕分ける必要がないため、作業効率が高いとされます。ただし、その場での仕分けにより、作業員の負担が増える可能性があります。
また、作業時間を短縮しようとすると、仕分けやピッキングのミスが起こりやすくなることも考慮すべきです。
人間がピッキング作業を行う上での問題点
ピッキング作業には、体力面や繰り返し作業、夜勤や繁忙期といった課題があります。作業員の体力や年齢によって疲労やミスが増え、作業効率が低下します。また、繰り返し作業では正確さが求められ、孤独感やミスのリスクが生じます。夜勤や繁忙期ではシフト制が採用され、作業時間が増えることもあります。
◇体力面
ピッキング作業を人間が行う上での主な問題点は、体力面です。作業担当者の年齢や運動習慣、筋肉量などによって体力は異なります。
このような体力を必要とする作業では、長時間の作業による疲労が作業効率の低下やミス増加につながることが考えられます。特に、商品棚まで移動して商品を取りに行く際の移動距離や、商品の重さによって体力消耗が変わります。
また、ピッキング作業の種類にかかわらず、作業員は常に迅速かつ正確に作業を行う必要があり、そのためには十分な体力が必要とされます。
◇繰り返し作業
ピッキング作業は、商品をピッキングして仕分けする単純な作業ですが、その過程で作業者は常に異なる商品を扱います。このような繰り返し作業は、作業者が商品の場所や種類を覚え、迅速かつ正確に処理する必要があります。
しかし、ピッキングの種類によっては、作業中はずっと一人で作業することがあり、他の人と接する機会が少ない環境もあります。このような状況は、作業者が孤独感を感じることもあり、また、慣れなどから生じるミスを増やす可能性もあります。
◇夜勤や繁忙期
倉庫や工場などでのピッキング作業は、場合によっては夜間作業が必要になることがあります。特に24時間稼働している場合は、2交代や3交代のシフト勤務が採用されることがあります。
普段は日勤だけであっても、繁忙期にはシフト勤務に切り替わることもよくあります。
人間とAMRのピッキングの違い
人間がピッキングを行う場合は、疲れや作業の単調さが問題です。作業効率が低下し、人件費や長時間労働の影響も考えられます。一方、AMRは自動的にピックアップし、作業効率が向上します。作業者は作業に集中し、リスクが低減します。
◇人間の場合
人間がピッキング作業を行う場合、作業担当者は商品をピックアップするために倉庫内を移動しなければなりません。そのため、歩行量が多くなり、長時間の作業によって疲れやストレスが溜まりやすくなります。
また、同じ作業を繰り返すことで単調さが生じ、注意力が低下し、ミスを誘発しやすいといわれています。
さらに、ピッキング作業は通常、作業者が用意されたリストを参照しながら行いますが、この方法は効率的とは言い難く、作業効率がよいとは言えません。リストに記載されている情報を読み取り、その商品を探し出すという手順が必要であり、作業者の集中力を削ぎます。加えて、目視での確認によるミスも避けられません。
また、人間が作業する場合は、人件費がかかるという費用面の問題も考えられます。
ピッキング作業の繁忙期や需要の高まりに対応するために作業時間が増加し、それに伴って人件費も増大します。さらに長時間の労働が発生する場合も多く、それは作業担当者の健康にも影響を及ぼす可能性があります。
◇AMRの場合
AMRがピッキング作業を担当する場合、倉庫管理システム(WMS)との連携が重要です。WMSから送られてくるピッキングリストを基に、AMRは自動的に商品棚へと移動します。作業担当者はAMRが到着した商品棚の前で待ち、AMRの画面に表示された商品をカゴに入れます。
ピッキングが完了したら、作業者はAMRに対してピッキング終了のボタンを押すことで、AMRは次の商品棚に向かいます。カゴが満杯になると、AMRは自動的に集荷場所に移動し、商品を下ろした後に次のピッキング先に向かいます。
このシステムにおいて、作業担当者はAMRの移動とピッキング作業に集中するだけでよいため、作業効率が向上し、作業時間が短縮されます。
さらに、WMSからの情報が直接AMRの画面に表示されるため、作業担当はリストの照合作業を行う必要がなく、作業ミスのリスクがほぼゼロになります。
ピッキングにAMRを導入して生産性アップ
工場や倉庫、店舗でのAMR導入は、作業担当者の負担軽減だけでなく、作業の効率化にもつながります。これにより、企業は利益向上に貢献することが期待されます。以下に、AMR導入のメリットを説明します。
◇作業時間の短縮
AMR導入のメリットのひとつは、作業時間の短縮です。
従来のピッキング作業では、作業者が商品を探すために移動する必要がありました。特に作業担当者の経験によっては、商品の位置を探すのに時間がかかることがあります。
しかし、AMRを導入すると、WMSと連動して商品棚に向かうため、作業担当者は移動するだけで済みます。これにより、作業時間が短縮され、作業効率が向上します。
◇作業ミスの減少
人間がピッキングする場合、人為的なミスを完全に避けることはできません。リストを目視で確認するため、見間違いにより違う商品棚に行ったり、間違った商品をカゴに入れてしまったりする可能性があります。
しかし、AMRを使用すると、WMSからの情報を元に商品棚へ行き、対象商品を作業担当者に表示するため、ピッキングミスのリスクが低くなります。
◇生産性の向上
AMRを導入することで、ピッキング作業の予測が容易になります。
従来の手動ピッキングでは、作業時間や作業者の能力によって作業の進捗が異なるため、繁忙期にどの程度の注文を処理できるかを正確に予測するのは難しい場合があります。
AMRは一貫したスピードで作業を行うため、注文の処理にかかる時間が予測しやすくなります。この予測を元に、繁忙期でもどの程度の注文量を処理できるかを見積もることができ、結果として生産性が向上します。
ピッキング作業は、商品を倉庫や工場から取り出す重要なプロセスです。シングルピッキングでは一人が一つずつ商品を取り出し、トータルピッキングでは複数の注文を一括して処理します。マルチオーダーピッキングは複数の注文を同時に処理しますが、ミスが起こりやすい傾向があります。
人間がピッキングを行う場合、体力面や繰り返し作業、夜勤などの課題があります。特に疲労や作業の単調さが作業効率を低下させる可能性があります。
一方、自動ガイドロボット(AMR)を導入すると、作業効率が向上し、作業ミスが減少します。作業者は移動とピッキングに集中し、作業効率が向上します。
AMRの導入により、作業時間が短縮され、作業ミスが減少し、生産性が向上することが期待されます。
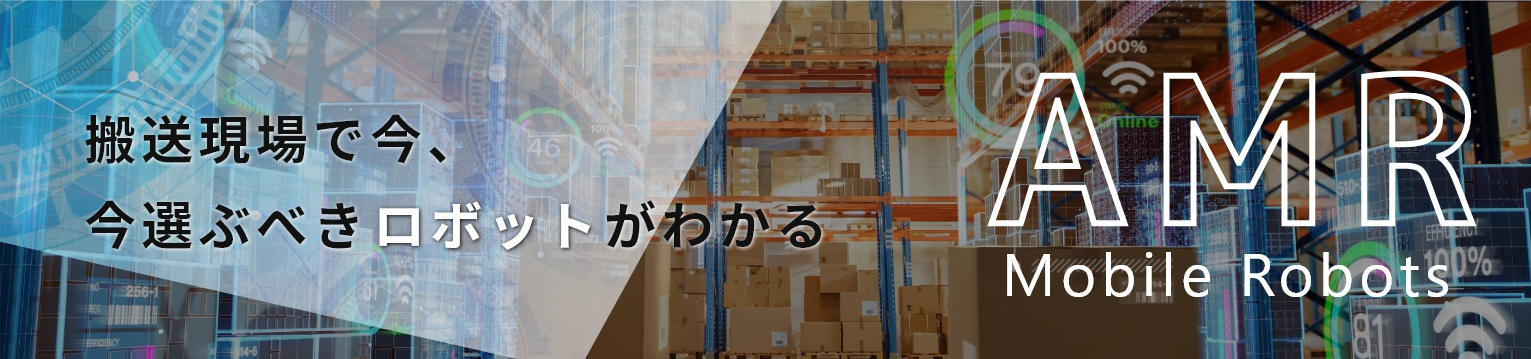